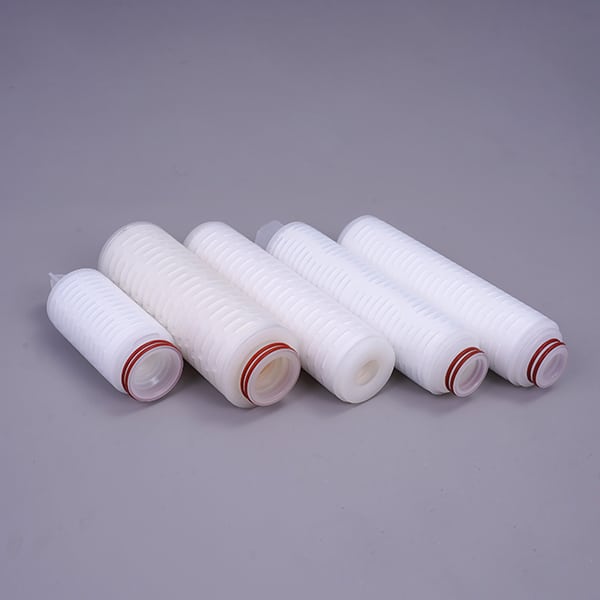
Comprehensive Guide to High-Efficiency Filtration: Maximizing Performance with 1 Micron to 1000 Micron Filters for Various Industries
Introduction
In today’s rapidly evolving industrial landscape, filtration has become a cornerstone of efficiency, safety, and operational success. From water treatment to food processing, and from pharmaceuticals to oil refinement, filters play a crucial role in maintaining the purity of liquids, gases, and other materials. With the right filtration system, companies can ensure high product quality, operational longevity, and cost savings.
This guide dives deep into the world of filters, focusing on various types such as 1 micron cloth, 100 micron mesh, and stainless steel filter mesh. Whether you’re in search of the finest filtration system like 1 micron stainless steel filters or require a more general-purpose filter such as a 200 micron nylon mesh, understanding micron ratings, filter materials, and mesh size is critical for optimal performance.
In this article, we will discuss the importance of filters ranging from 1 micron to 1000 micron, emphasizing their roles in various industries. Additionally, we’ll explore the benefits of different materials like nylon, stainless steel, and sintered wire mesh, giving you a comprehensive guide to selecting the right filter for your specific needs.
Chapter 1: Introduction to Micron and Mesh Filters
When it comes to filtration, understanding the difference between micron and mesh size is vital for choosing the correct filter for your application.
What is a Micron?
A micron, or micrometer, is a unit of measurement equal to one-millionth of a meter. In the context of filtration, microns measure the size of particles that a filter can trap. The smaller the micron rating, the finer the filtration. For instance, a 1 micron filter can capture extremely small particles such as bacteria and fine dust, whereas a 100 micron filter is designed for larger contaminants like sand and silt.
What is Mesh Size?
While micron ratings measure particle size, mesh size refers to the number of openings per linear inch in a filter. The higher the mesh size, the smaller the openings, making the filter capable of trapping finer particles. For example, a 100 mesh filter has 100 openings per inch, meaning it can filter out particles larger than 150 microns.
Common Uses of Micron and Mesh Filters
- 1 Micron Filters: Ideal for applications requiring ultra-fine filtration, such as in the pharmaceutical and water treatment industries.
- 10 Micron Filters: Commonly used in air filtration systems and for automotive applications.
- 100 Micron Filters: Frequently utilized in water filtration systems to remove sand, silt, and other larger contaminants.
- 200 Micron Filters: Often found in industrial applications where coarse filtration is required, such as in irrigation systems and pre-filtration stages.
Chapter 2: 1 Micron Filter Types and Applications
Filters with a 1 micron rating are some of the finest filters available on the market. They are capable of capturing extremely small particles and are typically used in industries where the highest level of filtration is required, such as pharmaceuticals, water purification, food processing, and electronics manufacturing. In this chapter, we will explore the various types of 1 micron filters, their applications, and the materials used to manufacture them.
1 Micron Cloth Filters
1 micron cloth filters are widely used in industries that require the removal of ultra-fine particles from liquids and gases. These cloth filters are often made from materials such as polypropylene, polyester, or nylon, which provide excellent filtration capabilities while remaining cost-effective. They are commonly used in liquid filtration systems, especially in industries like food and beverage, where purity is essential.
Key Applications:
- Water filtration: 1 micron cloth filters are often used in water purification systems to remove bacteria and other microscopic contaminants.
- Chemical filtration: In the chemical processing industry, these filters help remove fine particulates from chemical solutions, ensuring product purity.
- Food and beverage: Filters with this micron rating are used in brewing, winemaking, and other beverage production processes to ensure the final product is free of impurities.
1 Micron Mesh Filters
1 micron mesh filters are similar to cloth filters but use a woven mesh material to achieve filtration. These filters are often made from stainless steel, which provides durability and resistance to corrosion. Stainless steel mesh filters are especially popular in industries where high temperatures or harsh chemicals are involved.
Key Advantages:
- Durability: Stainless steel can withstand high temperatures and corrosive environments, making it ideal for industrial applications.
- Reusability: Unlike cloth filters, stainless steel mesh filters can often be cleaned and reused, making them a cost-effective option for long-term use.
- High precision: Mesh filters provide consistent and precise filtration, which is essential in industries like electronics manufacturing.
Applications of 1 Micron Mesh Filters:
- Pharmaceuticals: These filters are commonly used in the production of drugs and medical devices, where contamination must be avoided at all costs.
- Electronics: The manufacturing of semiconductors and other electronic components requires extremely pure environments, making 1 micron mesh filters essential.
- Food and beverage: Stainless steel mesh filters are used in processes like juice production, where fine particles need to be removed without compromising product quality.
1 Micron Screen Filters
1 micron screen filters are another common option for fine filtration. These filters are typically used in applications where both high filtration precision and durability are required. Like mesh filters, screen filters are often made from stainless steel or other durable materials.
Applications of 1 Micron Screen Filters:
- Water treatment: Screen filters are used in both residential and industrial water treatment systems to remove small particles and ensure clean water.
- Oil and gas industry: In the oil and gas sector, 1 micron screen filters are used to filter out fine particulates from fluids and gases, improving efficiency and safety.
- Air filtration: Some 1 micron screen filters are designed for air filtration, particularly in environments where clean air is crucial, such as laboratories or clean rooms.
1 Micron Stainless Steel Filters
1 micron stainless steel filters are among the most durable and reliable filtration options available. They are often used in industries where longevity and resistance to harsh environments are critical. Stainless steel filters provide excellent filtration efficiency while being able to withstand high pressure and temperature conditions.
Key Benefits:
- Corrosion resistance: Stainless steel’s natural resistance to corrosion makes these filters ideal for applications involving harsh chemicals or saltwater.
- Long life cycle: Stainless steel filters have a longer life span than other materials like nylon or polyester, reducing the need for frequent replacements.
- Heat resistance: These filters can handle high temperatures, making them suitable for use in industrial processes that involve heat.
Common Applications:
- Industrial filtration: These filters are used in industrial systems that require the removal of very fine particles from liquids and gases, such as in the oil and gas industry or chemical processing.
- Food production: Stainless steel filters are preferred in food production due to their resistance to corrosion and ease of cleaning, ensuring the hygiene of the filtration process.
- Water treatment: Stainless steel filters are widely used in water treatment plants, especially for desalination and filtration of seawater.
Chapter 3: Filters in the 10 to 100 Micron Range
Filters in the 10 to 100 micron range are essential for medium-grade filtration. These filters are widely used in industries where both small and relatively large particles need to be filtered out. Their versatility makes them popular in automotive, food processing, water treatment, and air filtration industries.
10 Micron Filters
10 micron filters are commonly used in applications where fine particles need to be removed but not as fine as those captured by 1 micron filters. These filters are available in a variety of materials, including nylon, polyester, and stainless steel. 10 micron filter cloth is especially popular for liquid filtration in the food and beverage industry.
Key Applications of 10 Micron Filters:
- Air filtration: 10 micron filters are often used in HVAC systems to remove dust and small particulates from the air, improving indoor air quality.
- Water treatment: In water filtration systems, 10 micron filters are used to remove small particles such as sand, silt, and algae.
- Automotive: 10 micron filters are commonly used in fuel filtration systems to remove fine particles from fuel, ensuring that engines run smoothly and efficiently.
100 Micron Filters
100 micron filters are used in a wide range of applications, particularly for coarse filtration where larger particles need to be removed. These filters are commonly made from materials like stainless steel and nylon, and are available in various forms, such as mesh filters, cloth filters, and screen filters.
Advantages of 100 Micron Filters:
- High flow rate: Since these filters have relatively large openings, they allow for a higher flow rate compared to finer filters, making them ideal for applications where volume is more important than precision.
- Durability: Stainless steel 100 micron filters are incredibly durable and can withstand harsh conditions, making them suitable for industrial and agricultural applications.
- Low maintenance: These filters typically require less frequent cleaning and replacement compared to finer filters, reducing downtime and maintenance costs.
Applications of 100 Micron Filters:
- Water filtration: 100 micron water filters are commonly used in irrigation systems to remove debris, preventing clogs and ensuring the efficient operation of sprinklers and other irrigation equipment.
- Hydraulic systems: In hydraulic systems, 100 mesh 200 sq in hydraulic filters are used to filter out particles from hydraulic fluid, preventing contamination and prolonging the life of hydraulic components.
- Oil and gas industry: These filters are used to filter out large particles from fluids and gases, improving the efficiency and safety of the filtration process.
Chapter 4: 100 to 200 Micron Filters for Medium Filtration
100 to 200 micron filters provide a balance between filtration precision and flow rate. They are widely used in systems that require the removal of medium-sized particles from liquids or gases. These filters are particularly popular in industries such as agriculture, oil and gas, and industrial manufacturing.
100 Micron Filter Mesh
100 micron filter mesh is one of the most common types of filters used for medium filtration. These filters are typically made from materials like nylon or stainless steel, depending on the application. 100 micron nylon filter cloth is often used in industries where chemical resistance is important, while 100 micron stainless steel mesh is preferred in harsh environments.
Key Advantages:
- Versatility: These filters are suitable for a wide range of applications, from water filtration to industrial processing.
- Cost-effective: Nylon and stainless steel mesh filters provide a cost-effective solution for medium filtration without compromising on performance.
- Easy to clean: Nylon and stainless steel filters are both easy to clean and maintain, reducing downtime and increasing efficiency.
Applications of 100 Micron Filter Mesh:
- Irrigation systems: 100 micron filters are commonly used in agricultural irrigation systems to remove particles that could clog sprinklers or drip lines.
- Water treatment: These filters are used in water treatment plants to remove medium-sized contaminants from water before it reaches the final filtration stage.
- Fuel filtration: In automotive and industrial fuel systems, 100 micron filters help remove large particles from fuel, ensuring clean combustion and reducing wear on engine components.
Chapter 5: 200 Micron Filters and Their Applications
Filters rated at 200 microns are used for applications that require medium to coarse filtration. They are particularly effective in removing larger particles while maintaining a high flow rate, making them ideal for industries like agriculture, water treatment, and industrial processing.
200 Micron Filter Mesh
200 micron filter mesh is commonly made from materials like nylon or stainless steel. These filters can handle a higher flow rate compared to finer filters, making them suitable for applications where volume is prioritized over precision.
Advantages of 200 Micron Filter Mesh:
- High flow rate: The larger openings in a 200 micron mesh allow liquids and gases to pass through at a higher rate, reducing the pressure drop across the filter.
- Durability: Stainless steel versions of 200 micron mesh are extremely durable and resistant to corrosion, ensuring a long service life in harsh environments.
- Easy maintenance: These filters are easy to clean and maintain, which is particularly beneficial in industries like agriculture and water treatment where downtime can be costly.
Applications of 200 Micron Filter Mesh:
- Irrigation systems: 200 micron irrigation filters are commonly used to filter out sand, silt, and other debris from irrigation water, preventing clogs in drip lines and sprinklers.
- Water filtration: These filters are widely used in pre-filtration stages in water treatment plants to remove larger particles before the water undergoes finer filtration processes.
- Industrial filtration: In industrial settings, 200 micron mesh is used to filter out larger particles from fluids and gases, ensuring the efficiency and longevity of machinery.
200 Micron Stainless Steel Filter Mesh
200 micron stainless steel filter mesh is a robust and reliable filtration solution, ideal for use in demanding environments. Its stainless steel construction makes it resistant to high temperatures and corrosive chemicals, ensuring long-term performance.
Key Benefits:
- Corrosion resistance: Stainless steel’s resistance to rust and corrosion makes it ideal for use in marine environments or chemical processing.
- Heat resistance: These filters can operate in high-temperature environments, making them suitable for industries such as oil refining and chemical manufacturing.
- Long lifespan: Stainless steel filters can be reused after cleaning, reducing the cost of replacement and maintenance over time.
Applications of 200 Micron Stainless Steel Filter Mesh:
- Oil and gas industry: Stainless steel filters are used to remove larger particles from crude oil and natural gas, ensuring the smooth operation of equipment and improving product quality.
- Chemical processing: These filters are employed in chemical plants to filter out solid particles from chemical solutions, preventing contamination and ensuring process efficiency.
- Food and beverage industry: Stainless steel filters are used in beverage production to remove particles from liquids such as juices, ensuring a smooth final product.
200 Micron Nylon Filter Cloth
200 micron nylon filter cloth is a versatile filtration medium used in industries that require chemical resistance, flexibility, and durability. Nylon is a popular material due to its excellent mechanical strength and resistance to chemicals, oils, and abrasion.
Advantages of Nylon Filter Cloth:
- Chemical resistance: Nylon filter cloth can withstand exposure to a wide range of chemicals, making it ideal for use in industries such as chemical processing and wastewater treatment.
- Flexibility: Nylon’s flexibility makes it easy to install in various filtration systems, from large industrial machines to smaller, portable filtration units.
- Cost-effective: Nylon filter cloth is an affordable filtration option that provides excellent performance for a wide range of applications.
Applications of 200 Micron Nylon Filter Cloth:
- Wastewater treatment: In wastewater treatment plants, 200 micron nylon filter cloth is used to filter out larger particles and debris from water before it undergoes finer filtration stages.
- Chemical processing: These filters are used in chemical plants to filter out impurities from solutions, ensuring product quality and process efficiency.
- Agriculture: Nylon filter cloth is commonly used in irrigation systems to prevent clogs in sprinklers and drip lines caused by sand and other debris.
Chapter 6: 1000 Micron Filters and Coarse Filtration
1000 micron filters are designed for coarse filtration, where the primary goal is to remove large particles from liquids or gases. These filters are commonly used in applications where the protection of downstream equipment is more important than the removal of fine particulates.
1000 Micron Mesh Filters
1000 micron mesh filters are often made from stainless steel, providing durability and resistance to corrosion. These filters are typically used in industries like oil and gas, agriculture, and water treatment, where large particles must be removed to protect equipment or improve efficiency.
Advantages of 1000 Micron Mesh Filters:
- High flow rate: Due to their large openings, 1000 micron mesh filters allow for a high flow rate, making them ideal for applications where large volumes of liquid or gas need to be filtered.
- Durability: Stainless steel mesh filters are resistant to corrosion, wear, and high temperatures, making them suitable for use in harsh environments.
- Low maintenance: These filters require less frequent cleaning and replacement compared to finer filters, reducing downtime and operational costs.
Applications of 1000 Micron Mesh Filters:
- Agricultural irrigation: In agricultural irrigation systems, 1000 micron filters are used to remove large debris such as leaves, twigs, and other organic matter from water before it reaches the irrigation lines.
- Oil and gas industry: These filters are used to protect equipment by removing large particles from fluids and gases, ensuring the smooth operation of pumps, valves, and other machinery.
- Water treatment: In water treatment plants, 1000 micron filters are used in pre-filtration stages to remove large particles before the water is treated with finer filters.
1000 Micron Strainers
1000 micron strainers are coarse filtration devices used to filter out large particles from liquids. These strainers are commonly made from materials like stainless steel and are used in industries that require the removal of debris from fluids to protect downstream equipment.
Advantages of 1000 Micron Strainers:
- High capacity: These strainers can handle large volumes of fluid while removing significant amounts of debris, making them ideal for use in high-flow systems.
- Durability: Stainless steel strainers are resistant to corrosion and wear, ensuring a long service life even in harsh environments.
- Ease of cleaning: These strainers are easy to clean and can be reused multiple times, reducing the need for frequent replacements.
Applications of 1000 Micron Strainers:
- Industrial filtration: In industrial settings, 1000 micron strainers are used to remove large particles from fluids, protecting equipment and ensuring process efficiency.
- Water treatment: These strainers are commonly used in water treatment systems to remove large debris from water before it undergoes finer filtration.
- Agriculture: 1000 micron strainers are used in irrigation systems to filter out large particles from water, ensuring the efficient operation of irrigation equipment.
Chapter 7: Fine and Medium Mesh Filters for Specific Applications
Fine and medium mesh filters, ranging from 5 microns to 500 microns, are widely used in industries where both filtration precision and high flow rates are important. These filters are commonly used in food and beverage processing, industrial manufacturing, and water treatment.
5 Micron Filters
5 micron filters are designed to capture very fine particles, making them ideal for industries that require high-precision filtration. These filters are typically made from materials like nylon, polyester, or stainless steel and are used in applications where purity is essential.
Applications of 5 Micron Filters:
- Food and beverage: These filters are used to remove fine particles from liquids like juices, beer, and wine, ensuring the final product is free from impurities.
- Water filtration: 5 micron filters are commonly used in water purification systems to remove fine particles, bacteria, and other contaminants.
- Pharmaceuticals: These filters are used in the production of drugs and medical devices, where even the smallest particles can affect product quality.
50 Micron Filter Mesh
50 micron filter mesh provide medium filtration and are used in a variety of industries where both particle removal and flow rate are important. These filters are commonly made from materials like nylon, stainless steel, and polyester.
Applications of 50 Micron Filters Mesh:
- Water treatment: 50 micron filters are used in water treatment plants to remove medium-sized particles from water before it undergoes finer filtration.
- Oil and gas: These filters are used to remove medium-sized particles from fluids in the oil and gas industry, protecting equipment and ensuring process efficiency.
- Agriculture: 50 micron filters are commonly used in irrigation systems to filter out medium-sized debris from water, preventing clogs in irrigation equipment.
Conclusion
Throughout this guide, we have explored the different types of filters and their specific applications across a variety of industries. Whether you’re looking for a 1 micron stainless steel mesh for fine filtration, or a 1000 micron strainer for coarse filtration, understanding the specific characteristics and advantages of each filter type can help you choose the right solution for your needs.
Chapter 8: Understanding Mesh and Micron Ratings for Effective Filtration
Before selecting the right filter for your application, it’s essential to understand the relationship between mesh sizes and micron ratings. The mesh size refers to the number of openings per inch in a filter screen, while the micron rating measures the diameter of particles a filter can capture.
Mesh and Micron Conversion
To give you an idea of how mesh sizes correlate with microns:
- 10 mesh is equivalent to 2000 microns
- 100 mesh is approximately 150 microns
- 200 mesh equals 74 microns
- 500 mesh is around 25 microns
As the mesh number increases, the number of openings per inch becomes finer, and the particle size that can pass through becomes smaller. Understanding these conversions can help you select the right filter for your application.
Selecting the Right Filter Based on Micron Rating
Choosing the right filter involves considering factors such as the size of the particles you need to filter, the flow rate of your system, and the environment in which the filter will operate.
- Fine filtration (below 10 microns): Used for applications where the removal of very small particles is critical, such as in the pharmaceutical or food and beverage industries.
- Medium filtration (10 to 100 microns): Suitable for water treatment, chemical processing, and oil and gas applications where both flow rate and particle removal are important.
- Coarse filtration (above 100 microns): Ideal for applications like irrigation, large-scale water treatment, and industrial manufacturing, where removing large debris or contaminants is the primary goal.
Importance of Mesh and Micron Rating in Different Applications
In industrial filtration, the mesh and micron rating will determine the filter’s efficiency in removing unwanted particles. For example, in irrigation systems, a 200 mesh filter, which corresponds to 74 microns, is effective at removing sand and small debris while allowing for high water flow. In contrast, for pharmaceutical production, a 5 micron filter would be used to ensure that even the smallest contaminants are removed to maintain product purity.
Key Factors to Consider:
- Flow Rate: Coarser filters allow for higher flow rates, making them ideal for applications like irrigation or industrial processes where large volumes of liquid need to pass through the filter quickly.
- Filter Durability: Stainless steel filters, especially those rated between 100 microns and 500 microns, offer high durability and resistance to corrosion, making them suitable for harsh environments like chemical processing.
- Particle Size: If your process involves removing large particles, such as leaves or sand, a 1000 micron filter would be appropriate. On the other hand, for finer filtration, such as removing bacteria from water, a 1 micron filter would be necessary.
Chapter 9: Application-Specific Insights and Case Studies
In this chapter, we will explore some industry-specific case studies that illustrate how different mesh and micron filters are used in practice. These examples demonstrate how selecting the right filter can improve operational efficiency, product quality, and equipment longevity.
Case Study 1: Irrigation and Agricultural Use
In an agricultural setting, where large volumes of water are used to irrigate crops, maintaining clean water is essential for preventing clogs in drip lines and ensuring the health of plants. A 200 micron irrigation filter was used in a large-scale farm to filter out sand and small debris from water. The stainless steel version of the filter was chosen for its durability and ability to withstand outdoor conditions. This system allowed the farm to increase the efficiency of its irrigation system, reducing the need for maintenance and minimizing downtime due to clogs.
Key Results:
- Improved water flow due to reduced clogging
- Lower maintenance costs due to the durability of the filter
- Consistent irrigation, leading to healthier crops
Case Study 2: Water Treatment in Municipal Systems
A municipal water treatment facility needed to improve its filtration process to remove larger contaminants before water entered the finer filtration stages. The facility selected a combination of 100 micron mesh and 50 micron stainless steel filters to capture debris like sediment and organic matter. This pre-filtration stage helped extend the life of the finer filters used later in the process, improving overall system efficiency and reducing operational costs.
Key Results:
- Prolonged lifespan of finer filters
- Enhanced water quality in the pre-filtration stage
- Reduced energy costs due to improved system efficiency
Case Study 3: Oil and Gas Industry
In the oil and gas industry, filtration plays a crucial role in protecting equipment and ensuring the quality of the extracted product. A 1000 micron stainless steel mesh filter was used to remove large particles from crude oil, preventing damage to pumps and valves during the refining process. Additionally, 5 micron mesh filters were used in the final stages of filtration to remove finer impurities, ensuring a high-quality final product.
Key Results:
- Protection of critical equipment, reducing maintenance and replacement costs
- Improved product quality, leading to higher profitability
- Enhanced system performance due to the removal of large particles early in the process
Chapter 10: Maintenance and Best Practices for Prolonging Filter Life
Regardless of the filter size or material, proper maintenance is essential for ensuring long-term performance. Regular cleaning and inspection of filters will help prevent clogs and ensure that the filtration system operates at optimal efficiency.
Cleaning Mesh Filters
Most mesh filters, especially those made from durable materials like stainless steel or nylon, can be cleaned and reused. The frequency of cleaning will depend on the type of material being filtered and the environment in which the filter operates.
Steps for Cleaning:
- Rinse with water: For most applications, a thorough rinse with clean water will remove trapped particles.
- Use compressed air: If particles are deeply embedded in the mesh, compressed air can be used to blow them out of the filter.
- Chemical cleaning: For filters used in chemical or oil industries, it may be necessary to use a cleaning solution to dissolve any build-up.
Replacing Worn Filters
Even the most durable filters, such as those made from stainless steel, will eventually need to be replaced. Signs that a filter needs replacement include:
- Reduced flow rate: A noticeable decrease in flow rate indicates that the filter is becoming clogged and can no longer effectively remove particles.
- Visible damage: Tears, holes, or warping in the mesh signal that the filter can no longer provide effective filtration.
Chapter 11: Future Trends in Filtration Technology
Filtration technology continues to evolve, with innovations aimed at improving efficiency, reducing costs, and enhancing the sustainability of filtration systems. In this final chapter, we will explore some of the latest trends in filtration technology and how they are shaping the future of industries like water treatment, food and beverage processing, and chemical manufacturing.
Nano-Filtration Technologies
One of the most exciting developments in filtration technology is the emergence of nano-filtration. These filters can remove particles as small as 0.001 microns, making them ideal for industries that require ultra-fine filtration. Applications include the removal of viruses, bacteria, and other microscopic contaminants from water and medical products.
Smart Filtration Systems
Smart filtration systems use sensors and automated controls to monitor filter performance in real-time. These systems can detect when a filter is becoming clogged and trigger maintenance alerts, ensuring that filters are cleaned or replaced before they cause a problem. This technology is particularly useful in large-scale industrial applications where downtime can be costly.
Sustainable Filter Materials
As industries place a greater emphasis on sustainability, there is growing interest in using biodegradable or recyclable filter materials. Research is underway to develop filters made from organic materials that can be easily broken down after use, reducing the environmental impact of industrial filtration processes.
Conclusion
Understanding the various types of filters, from 1 micron mesh screens to 1000 micron strainers, is critical for selecting the right filtration solution for your industry. With advancements in filtration technology, industries will continue to see improvements in efficiency, product quality, and sustainability. Whether you’re working in water treatment, agriculture, or industrial manufacturing, choosing the right filter will ensure the long-term success of your filtration system.
Chapter 12: Comparison of Different Filter Materials
Selecting the correct filter material is essential to achieve the desired filtration performance in various industries. Different materials, such as nylon, stainless steel, and polypropylene, offer distinct advantages and limitations depending on the environment and application. In this chapter, we will compare these materials to help you make an informed decision for your specific filtration needs.
Nylon Filters
Nylon mesh is commonly used in applications that require fine filtration, as it offers excellent chemical resistance and durability. Nylon filters are ideal for filtering fine particles in water treatment, food processing, and pharmaceutical applications.
Advantages:
- High tensile strength, offering longevity
- Resistant to a wide range of chemicals, making it ideal for chemical filtration
- Suitable for both dry and liquid filtration
Disadvantages:
- Nylon can absorb moisture over time, which may alter its properties
- May degrade if exposed to harsh environments such as extreme UV radiation or high temperatures
Common Applications:
- 200 micron nylon mesh is widely used in irrigation systems to filter out small debris
- 20 micron nylon mesh is suitable for fine filtration in food and beverage industries
- 100 micron nylon mesh is often used in medical and laboratory settings for precise filtration needs
Stainless Steel Filters
Stainless steel is a highly durable material often used in demanding industrial environments. It offers excellent resistance to corrosion, high temperatures, and pressure, making it suitable for applications that involve extreme conditions.
Advantages:
- Excellent resistance to corrosion and high temperatures
- Durable, allowing for long-term use in harsh environments
- Easy to clean and reuse, reducing operational costs
Disadvantages:
- Higher initial cost compared to other materials
- Can be more challenging to work with in terms of fabrication and customization
Common Applications:
- 100 micron stainless steel filters are used in hydraulic systems to remove debris and contaminants from fluids
- 5 micron stainless steel mesh filters are popular in chemical processing, oil and gas, and pharmaceutical applications where precision filtration is essential
- 10 micron stainless steel filter screens are used in wastewater treatment and food production facilities
Polypropylene Filters
Polypropylene (PP) filters are widely used in industries such as water treatment, chemical processing, and food production. These filters are known for their resistance to a variety of chemicals and their lightweight, cost-effective nature.
Advantages:
- Highly resistant to chemicals, acids, and bases
- Lightweight and cost-effective for large-scale filtration
- Suitable for disposable applications
Disadvantages:
- Limited resistance to high temperatures compared to stainless steel
- Can become brittle over time, especially in UV-exposed environments
Common Applications:
- 50 micron polypropylene filters are widely used in water treatment plants to filter sediment from water
- 100 micron polypropylene mesh is used in food production to remove larger particles while maintaining high flow rates
- 10 micron polypropylene filters are common in pharmaceutical applications where chemical compatibility and cost-effectiveness are critical
Chapter 13: Environmental Impact of Filter Materials
As industries worldwide are increasingly concerned about sustainability, understanding the environmental impact of different filter materials has become crucial. This chapter will explore the ecological considerations associated with nylon, stainless steel, and polypropylene filters, offering guidance on how to minimize their environmental footprint.
Nylon Filters and Environmental Impact
Nylon is a synthetic polymer that is not biodegradable, making its environmental impact a concern for industries aiming to reduce their waste output. However, nylon filters are often washable and reusable, which can help reduce the number of discarded filters over time.
Ways to Reduce Impact:
- Extend the lifespan of nylon filters through proper maintenance and cleaning
- Implement recycling programs for worn-out nylon filters
Stainless Steel Filters and Environmental Impact
Stainless steel is highly durable and recyclable, making it one of the more environmentally friendly options. Although the initial production of stainless steel is energy-intensive, its long lifespan and recyclability make it an excellent choice for reducing waste.
Ways to Reduce Impact:
- Recycle stainless steel filters after their usable life has ended
- Invest in high-quality filters that will last longer, reducing the need for replacements
Polypropylene Filters and Environmental Impact
Polypropylene is a plastic polymer that can contribute to environmental pollution if not properly managed. However, because PP filters are often disposable and lightweight, they are more cost-effective for industries that require frequent replacements. The challenge is ensuring that used polypropylene filters are disposed of responsibly.
Ways to Reduce Impact:
- Use polypropylene filters in applications where disposability is crucial, but ensure responsible disposal methods, such as incineration or recycling when possible
- Opt for reusable filter alternatives whenever feasible to reduce waste output
Chapter 14: Cost Considerations and ROI for Filter Selections
The selection of a filter system not only depends on its filtration efficiency and environmental impact but also on the cost and return on investment (ROI). In this chapter, we will examine the cost considerations for different filter types and provide insights on how to calculate the long-term ROI.
Nylon Filters: Balancing Cost and Performance
Nylon filters are generally affordable and offer good performance across various industries. Their reusability makes them a cost-effective choice for applications that require frequent filtration without compromising on particle retention capabilities.
Cost Breakdown:
- Initial cost: Relatively low compared to stainless steel options
- Maintenance cost: Moderate, as nylon filters can often be cleaned and reused
- Replacement frequency: Low to moderate, depending on the application and maintenance
ROI Factors:
- The initial investment in nylon filters is relatively low, and their reusability offers cost savings over time, especially in medium-duty filtration applications like food production and irrigation.
Stainless Steel Filters: A Premium for Longevity
Stainless steel filters come with a higher upfront cost but are known for their long-lasting durability. These filters offer the best ROI for industries that require high-temperature resistance, chemical compatibility, and long-term durability.
Cost Breakdown:
- Initial cost: High due to the quality of the material
- Maintenance cost: Low, as stainless steel filters are highly durable and easy to clean
- Replacement frequency: Low, with filters lasting years in some applications
ROI Factors:
- While the upfront investment in stainless steel filters is high, the long lifespan and minimal replacement frequency make them highly cost-effective for industries like oil and gas, pharmaceuticals, and heavy-duty industrial applications.
Polypropylene Filters: Economical with Frequent Replacement
Polypropylene filters offer the lowest upfront cost, making them ideal for applications that require frequent filter changes or for industries that prioritize cost over longevity.
Cost Breakdown:
- Initial cost: Low, making them accessible for large-scale filtration systems
- Maintenance cost: High, due to the need for frequent replacements
- Replacement frequency: High, as PP filters are often disposable and used in one-time applications
ROI Factors:
- Polypropylene filters are cost-effective in applications where frequent filter changes are necessary, but their shorter lifespan can lead to higher long-term costs in industries that demand continuous, large-scale filtration.
Chapter 15: Filter System Integration and Customization Options
Selecting the right filter is only part of the equation—integrating it into your filtration system is equally important. In this chapter, we will explore how to customize and integrate filters based on specific application needs, flow rates, and environmental factors.
Customizing Filter Mesh Sizes
Customization allows industries to tailor filters to their unique filtration needs. For example, an 80 mesh filter may be suitable for irrigation systems to trap larger particles, while a 1 micron stainless steel filter may be used in pharmaceutical production to ensure the purity of liquid products.
Customization Options:
- Mesh size: Choose the appropriate mesh size based on particle size requirements
- Filter material: Select between nylon, stainless steel, and polypropylene depending on the application’s chemical and temperature resistance needs
- Filter housing: Customize filter housing to accommodate different sizes and materials, ensuring seamless integration into existing systems
Integrating Filters into Existing Systems
Proper integration ensures that filters work efficiently within a broader system, preventing bottlenecks or flow disruptions. When integrating filters, it’s essential to consider:
- Flow rate compatibility: Ensure the selected filter mesh can handle the system’s flow rate without causing pressure drops
- Environmental factors: If the system operates in a harsh environment, selecting a more durable filter material such as stainless steel is crucial
- Maintenance accessibility: Design systems that allow for easy access to filters for cleaning or replacement
Chapter 16: Conclusion and Final Recommendations
Filtration systems are integral to numerous industries, from water treatment to pharmaceuticals and food production. Selecting the right filter involves understanding key factors such as micron ratings, filter materials, and application requirements.
Chapter 17: Industry-Specific Applications and Case Studies
Understanding the practical applications of filtration systems across various industries can offer valuable insights into choosing the right filter. In this chapter, we will explore specific use cases in different sectors and provide examples of how filters have optimized operations, improved efficiency, and reduced costs.
Water Treatment Industry
In the water treatment industry, filtration plays a critical role in removing contaminants and ensuring safe drinking water. The use of 1 micron stainless steel mesh or 100 micron nylon filter cloth is common for filtering sediment, particulates, and impurities from raw water sources.
Case Study: Municipal Water Treatment Facility A municipal water treatment plant implemented a series of filters, including 10 micron stainless steel filter screens and 200 micron nylon mesh, to treat large volumes of water for public consumption. By strategically using filters with different micron ratings, the plant was able to remove large debris first, followed by finer filtration stages to ensure compliance with safety standards. As a result, the facility reduced maintenance costs by 30% due to the durability of the stainless steel filters and minimized filter replacements.
Key Takeaways:
- Multiple filtration stages ensure a thorough purification process
- Durable stainless steel filters provide long-term cost savings
- Different micron ratings can be used to tackle various particle sizes
Pharmaceutical Industry
In the pharmaceutical industry, maintaining purity during production is paramount. The use of 1 micron mesh screens and 5 micron stainless steel mesh filters ensures that liquids and gases are free of contaminants. These filters are often used in sterile environments where precision and reliability are critical.
Case Study: Sterile Drug Manufacturing A pharmaceutical company needed a reliable filtration system to remove bacteria and other contaminants during drug production. They opted for 1 micron stainless steel mesh filters to provide the highest level of filtration. Over time, this solution reduced contamination risks by 50% and improved product quality, ensuring regulatory compliance and boosting customer satisfaction.
Key Takeaways:
- High-efficiency filters like 1 micron stainless steel mesh ensure sterility
- Precision filtration reduces contamination and enhances product quality
- Proper filtration improves regulatory compliance
Food and Beverage Industry
In the food and beverage industry, filters are essential for ensuring product safety and quality. 10 micron nylon mesh and 5 micron nylon filter cloth are often used in processes like juice production and dairy processing, where removing solid particles and bacteria is crucial for preserving flavor and safety.
Case Study: Beverage Production A juice manufacturer required a filtration system to remove pulp and other solids without compromising the flavor. They installed a multi-stage filtration system using 200 micron nylon mesh for initial pulp removal and 10 micron filter mesh for final filtration. The result was a smooth, high-quality product with improved consistency, which increased customer satisfaction and led to a 15% rise in sales.
Key Takeaways:
- Multi-stage filtration ensures optimal product quality
- Nylon mesh filters effectively remove solids without impacting taste
- Improved filtration can lead to higher product consistency and sales
Oil and Gas Industry
The oil and gas industry relies on filtration systems to remove impurities from fluids and gases in harsh environments. 100 mesh 200 sq in hydraulic filters and 50 micron stainless steel filters are used to prevent damage to equipment and ensure efficient operation.
Case Study: Oil Refinery An oil refinery integrated 100 micron stainless steel filters into its processing system to remove contaminants from crude oil. The filters’ durability and resistance to high temperatures resulted in fewer shutdowns, reduced maintenance costs, and increased operational efficiency by 20%.
Key Takeaways:
- Stainless steel filters withstand harsh conditions and high temperatures
- Filtration improves equipment longevity and reduces operational costs
- Efficient filtration systems reduce downtime in industrial settings
Chapter 18: Best Practices for Filter Maintenance
Proper filter maintenance is critical for ensuring long-lasting performance and avoiding unnecessary replacements. This chapter will provide tips for maintaining filters, including cleaning protocols, inspection schedules, and common troubleshooting techniques.
Cleaning Procedures
Depending on the filter material, cleaning processes vary. Stainless steel filters can typically be washed and reused, while nylon and polypropylene filters may need more delicate handling.
Best Practices:
- Stainless steel filters: Clean with water or mild detergents, followed by drying to avoid rust formation
- Nylon filters: Rinse with water or a gentle cleaning solution; avoid harsh chemicals that could damage the mesh
- Polypropylene filters: Disposable filters should be replaced according to the manufacturer’s guidelines; reusable ones can be cleaned with mild detergents
Inspection and Replacement Schedules
To maximize the lifespan of filters, it’s important to conduct regular inspections to check for wear and tear, clogging, or damage. Here are some guidelines:
- Daily inspections for critical systems like pharmaceuticals and food production to avoid contamination
- Weekly or monthly checks for water treatment and industrial systems, depending on usage frequency
When to Replace a Filter:
- When there is a noticeable decrease in flow rate
- If cleaning no longer restores the filter’s efficiency
- Visible damage or significant wear
Chapter 19: Custom Filter Solutions and Vendor Selection
Selecting the right vendor and customizing filters to fit your system can greatly impact overall efficiency. This chapter will guide you through the process of sourcing high-quality filters and designing custom solutions that match your operational needs.
Choosing the Right Vendor
When sourcing filters, quality and reliability are paramount. Consider vendors that offer:
- A broad range of materials (nylon, stainless steel, polypropylene)
- Customization options for specific micron ratings and sizes
- Technical support for system integration
Vendor Checklist:
- Experience: Ensure the vendor has a proven track record in your industry
- Certifications: Look for ISO certifications and other quality assurance marks
- Support: Choose a vendor that offers after-sales support and guidance
Designing Custom Filters
For specialized applications, standard filters may not be enough. Custom filters can be tailored to specific micron ratings, flow rates, and operating conditions. Working with a knowledgeable vendor, you can design filters that perfectly fit your system, minimizing downtime and maximizing filtration efficiency.
Customization Considerations:
- Mesh size: Choose between fine mesh for precision filtration (e.g., 1 micron mesh filter) and coarser mesh for higher flow rates (e.g., 100 micron screen filter)
- Material: Select materials based on chemical resistance, temperature, and durability needs
- System compatibility: Ensure the filter design integrates smoothly into your existing system, considering factors like housing size and maintenance accessibility
Chapter 20: The Future of Filtration Technologies
The filtration industry is evolving, with new technologies emerging to improve efficiency, sustainability, and precision. In this final chapter, we will explore some of the latest advancements in filtration and how they can benefit various industries.
Nanotechnology in Filtration
Nanotechnology is revolutionizing filtration by creating ultra-fine filters capable of trapping even the smallest particles. Nanofilters can be made from advanced materials like carbon nanotubes, offering unprecedented filtration efficiency.
Benefits of Nanofilters:
- Higher precision, capable of filtering down to the molecular level
- Potential applications in industries like pharmaceuticals and water purification
- Greater efficiency with smaller filter sizes, reducing material use
Smart Filtration Systems
The rise of the Internet of Things (IoT) is enabling the development of smart filtration systems that monitor performance in real-time. These systems can detect clogs, track usage, and send maintenance alerts, reducing downtime and improving operational efficiency.
Key Features:
- Real-time monitoring and alerts
- Automated cleaning or replacement reminders
- Data tracking for improved system optimization
Sustainable Filtration Solutions
As industries become more focused on sustainability, filtration technologies are adapting to meet these goals. Innovations include reusable filter materials, more efficient designs that reduce energy consumption, and filters made from biodegradable materials.
Eco-friendly Advancements:
- Recyclable materials like stainless steel and nylon
- Low-energy filtration systems that reduce operational costs
- Biodegradable filters made from natural fibers for one-time-use applications
Conclusion: Maximizing Filtration Efficiency
Choosing the right filtration system requires careful consideration of your industry’s specific needs, operational environment, and sustainability goals. From 1 micron stainless steel filters to 100 micron nylon mesh, the wide variety of available options allows industries to tailor filtration systems to their exact requirements. By selecting the correct filters, integrating them effectively, and maintaining them properly, you can ensure that your filtration system operates at peak efficiency, delivering clean, safe, and high-quality outputs across a range of applications.
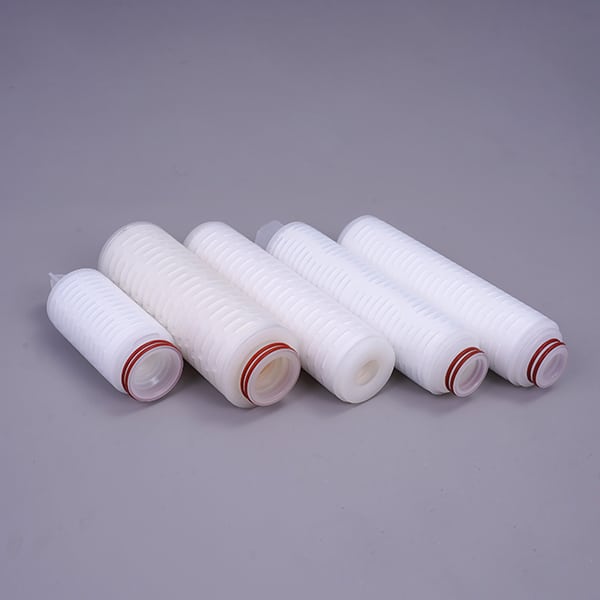