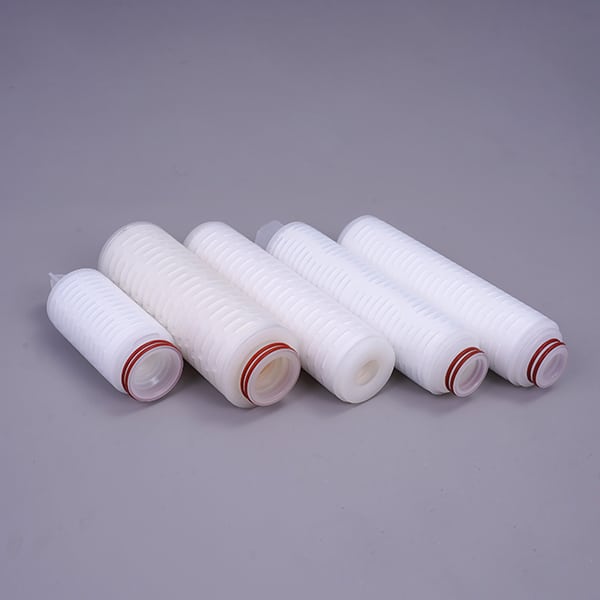
Different Types of Liquid Filter Cartridges: Understanding Your Options
When it comes to liquid filtration, selecting the appropriate filter cartridge is critical for ensuring optimal performance in various applications, whether for industrial purposes or everyday use. There are several types of liquid filter cartridges available, each designed to handle different filtration needs based on the type of liquid, the level of purity required, and the contaminants involved. Below is an in-depth exploration of the different types of liquid filter cartridges and how they can be used in various industries.
1. Melt Blown Filter Cartridges
Melt blown filter cartridges are a highly efficient choice for depth filtration. These cartridges are constructed using layers of polypropylene, thermally bonded to create a dense and uniform structure. This design allows for high dirt-holding capacity and effective contaminant removal from liquids.
Melt blown cartridges are particularly popular in industries that require filtration of fine particles and high purity. Applications include the food and beverage industry, potable water systems, and industrial process water. Their versatile nature makes them suitable for a range of filtration requirements from 1 to 100 microns, making them ideal for trapping both coarse and fine contaminants.
2. String Wound Filter Cartridges
String wound cartridges offer an economical option for liquid filtration and are designed for use in industries requiring depth filtration. These cartridges consist of a central core wrapped with a string made of various materials such as cotton, nylon, or polypropylene. The pattern of the winding creates a diamond-shaped lattice that effectively captures particles.
String wound filter cartridges can handle a broad range of liquids and are commonly used for filtering potable water, chemicals, cosmetics, and cleaning fluids. Their ability to manage dirt loads effectively without significant pressure loss makes them ideal for high-flow applications.
3. Pleated Filter Cartridges
Pleated filter cartridges come in two main varieties: nominal depth pleated and economy grade pleated filters. Both types use pleated media to increase surface area, providing a higher dirt-holding capacity compared to non-pleated options. Nominal depth pleated filters are particularly beneficial in high-flow applications where maintaining a low-pressure drop is important. These cartridges are widely used in industries such as food and beverage, coatings, and liquid filtration where uniform particle size is a key concern.
Economy grade pleated cartridges offer a cost-effective option for applications where fine sediment removal is necessary. They are often used in potable water systems, chemicals, and general industrial applications.
4. Membrane Filter Cartridges
Membrane filter cartridges are the highest purity option available, often used in critical applications that demand the removal of ultra-fine particles and microorganisms. Membrane filters are designed to remove contaminants as small as 0.01 microns, making them suitable for pharmaceutical manufacturing, fermentation processes, and deionized water filtration.
These cartridges are flushed with high-purity water during manufacturing and meet stringent requirements for extractables, ensuring that no undesirable residues are introduced into the filtered liquid. Industries such as winemaking, brewing, and juice production also rely on membrane filters for clarifying liquids and ensuring product quality.
5. Activated Carbon Filter Cartridges
Activated carbon filters are essential for removing chlorine, volatile organic compounds (VOCs), and other chemical contaminants from liquids. These filters are commonly used in water purification systems to improve taste and odor. Activated carbon cartridges are also popular in industries such as food and beverage, where removing impurities that affect flavor is important. They are effective at reducing harmful substances without affecting the flow rate or causing significant pressure drop.
Factors to Consider When Choosing a Filter Cartridge
1. Micron Rating
The micron rating of a filter cartridge determines the size of the particles it can capture. For example, a 1-micron filter will trap particles as small as 1 micron. Filters with a lower micron rating are used for finer filtration, while higher micron ratings are suited for removing larger particles.
It is important to select a filter with the appropriate micron rating based on the level of filtration required by your specific application. For instance, food and beverage industries often require filters with a micron rating between 1 to 100, while pharmaceutical industries may need cartridges rated as low as 0.01 microns for sterile filtration.
2. Material Compatibility
Different filter cartridges are made from various materials, including polypropylene, polyester, nylon, and cotton. The choice of material is crucial for ensuring that the filter is compatible with the liquid being filtered. For instance, polypropylene is highly resistant to chemicals and can be used in a wide range of industrial applications, while nylon filters are preferred for high-temperature and high-purity applications.
3. Flow Rate and Pressure Drop
The efficiency of a filter cartridge is also influenced by the flow rate and the pressure drop across the filter. A filter with a higher dirt-holding capacity will last longer and provide more consistent performance, even as contaminants accumulate. Pleated cartridges typically offer a lower initial pressure drop and are ideal for applications that require high flow rates without sacrificing filtration efficiency.
Conclusion
Selecting the right liquid filter cartridge depends on several factors, including the type of contaminants present, the required purity of the liquid, and the specific conditions of the filtration system. Whether you need a cost-effective solution for general liquid filtration or a high-purity membrane filter for sensitive applications, understanding the various types of filter cartridges will help you make an informed decision. By choosing the appropriate filter for your application, you can ensure the highest levels of performance, efficiency, and product quality.
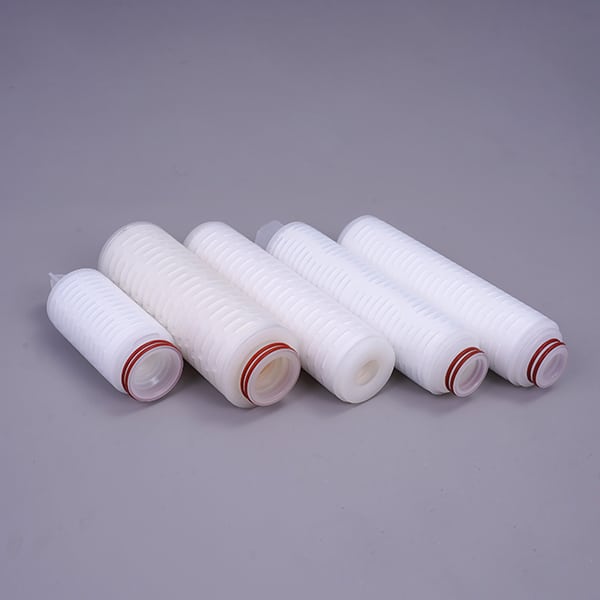