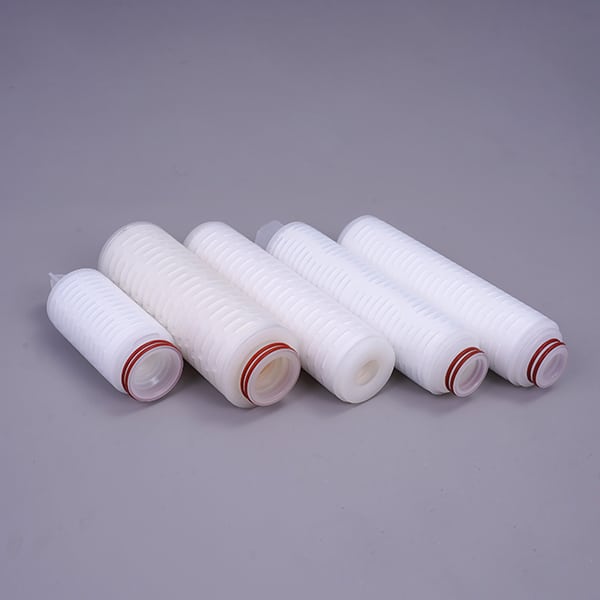
High Flow Filter Elements: The Backbone of Industrial Filtration
Benefits of Using High Flow Filter Elements in Industrial Filtration Systems
High flow filter elements play a crucial role in industrial filtration systems, serving as the backbone of the entire process. These filter elements are designed to handle high flow rates while effectively removing contaminants from liquids and gases. By using high flow filter elements, industrial facilities can ensure the quality of their products, protect equipment from damage, and comply with regulatory standards.
One of the key benefits of using high flow filter elements is their ability to handle large volumes of fluid without sacrificing filtration efficiency. Traditional filter elements may struggle to keep up with high flow rates, leading to clogging and reduced performance. High flow filter elements, on the other hand, are specifically engineered to handle high flow rates while maintaining their filtration capabilities. This ensures that contaminants are effectively removed from the fluid stream, regardless of the volume being processed.
In addition to their high flow capacity, high flow filter elements also offer superior filtration efficiency. These filter elements are designed to capture a wide range of contaminants, including particles, debris, and microorganisms. By effectively removing these contaminants from the fluid stream, high flow filter elements help to improve product quality and protect downstream equipment from damage. This is particularly important in industries such as food and beverage, pharmaceuticals, and electronics manufacturing, where product purity is critical.
Another benefit of using high flow filter elements is their long service life. These filter elements are constructed from durable materials that can withstand high flow rates and harsh operating conditions. As a result, high flow filter elements require less frequent replacement compared to traditional filter elements, reducing maintenance costs and downtime. This not only saves money but also ensures that the filtration system operates at peak efficiency for longer periods of time.
Furthermore, high flow filter elements are easy to install and maintain, making them a cost-effective solution for industrial filtration systems. These filter elements can be quickly replaced when needed, minimizing downtime and ensuring continuous operation. Additionally, high flow filter elements are designed to be compatible with a wide range of filtration systems, making them a versatile option for various industrial applications.
In conclusion, high flow filter elements are an essential component of industrial filtration systems, offering numerous benefits to users. From their high flow capacity and superior filtration efficiency to their long service life and ease of maintenance, high flow filter elements provide a cost-effective solution for ensuring product quality, protecting equipment, and meeting regulatory standards. By incorporating high flow filter elements into their filtration systems, industrial facilities can improve operational efficiency, reduce maintenance costs, and achieve optimal filtration performance.
How High Flow Filter Elements Improve Efficiency and Performance in Industrial Applications
High flow filter elements play a crucial role in industrial filtration systems, serving as the backbone that ensures efficiency and performance. These filter elements are designed to handle high flow rates while effectively removing contaminants from various fluids, such as water, oil, and gas. By understanding how high flow filter elements work and their benefits, industrial applications can achieve optimal filtration results.
One of the key advantages of high flow filter elements is their ability to handle large volumes of fluid without compromising filtration efficiency. Traditional filter elements may struggle to keep up with high flow rates, leading to reduced filtration performance and potential system failures. High flow filter elements, on the other hand, are specifically engineered to handle high flow rates while maintaining high levels of filtration efficiency. This ensures that contaminants are effectively removed from the fluid stream, protecting downstream equipment and processes.
In addition to their high flow capacity, high flow filter elements are also designed for easy maintenance and replacement. Industrial applications often require frequent filter changes to ensure optimal performance, and the ease of replacing high flow filter elements can help minimize downtime and maintenance costs. With quick and simple replacement procedures, operators can easily swap out filter elements without disrupting operations, keeping the filtration system running smoothly.
Furthermore, high flow filter elements are available in a variety of materials and configurations to suit different industrial applications. Whether filtering water for cooling systems, oil for lubrication, or gas for processing, there is a high flow filter element that meets the specific requirements of each application. From pleated filter media to depth filter cartridges, industrial users can choose the right filter element to achieve the desired level of filtration performance.
Another benefit of high flow filter elements is their longevity and durability. Industrial environments can be harsh and demanding, putting filter elements under constant stress. High flow filter elements are built to withstand these challenging conditions, with robust construction and high-quality materials that ensure long-lasting performance. By investing in high flow filter elements, industrial applications can reduce the frequency of filter replacements and maintenance, saving time and money in the long run.
Overall, high flow filter elements are essential components of industrial filtration systems, providing the efficiency and performance needed to maintain optimal operation. With their ability to handle high flow rates, easy maintenance and replacement, versatility in materials and configurations, and durability in harsh environments, high flow filter elements offer a reliable solution for industrial filtration needs. By incorporating high flow filter elements into their systems, industrial applications can achieve superior filtration results and ensure the smooth operation of their processes.
Types of High Flow Filter Elements Available for Different Industrial Filtration Needs
High Flow Filter Elements: The Backbone of Industrial Filtration
When it comes to industrial filtration, high flow filter elements play a crucial role in ensuring the efficiency and effectiveness of the filtration process. These filter elements are designed to handle large volumes of fluid while maintaining high levels of filtration performance. In this section, we will explore the different types of high flow filter elements available for various industrial filtration needs.
One of the most common types of high flow filter elements is the pleated filter cartridge. These cartridges are made up of a pleated filter media that provides a large surface area for filtration. The pleated design allows for increased dirt-holding capacity, which means that these filter elements can handle higher flow rates for longer periods without compromising filtration efficiency. Pleated filter cartridges are widely used in applications such as water treatment, chemical processing, and oil and gas industries.
Another type of high flow filter element is the bag filter. Bag filters are typically made of a porous material that allows fluid to pass through while capturing solid particles. These filters are known for their high dirt-holding capacity and are commonly used in applications where large volumes of fluid need to be filtered. Bag filters are often used in industries such as food and beverage, pharmaceuticals, and wastewater treatment.
In addition to pleated filter cartridges and bag filters, there are also high flow filter elements known as depth filters. Depth filters are made up of a thick layer of filter media that captures particles throughout its depth. This design allows for a higher dirt-holding capacity and longer service life compared to other types of filters. Depth filters are commonly used in applications where high levels of filtration efficiency are required, such as in the electronics and semiconductor industries.
For applications that require the removal of oil and water from compressed air or gas, coalescing filter elements are the ideal choice. These filter elements are designed to capture and separate liquid droplets from the gas stream, ensuring clean and dry air or gas output. Coalescing filter elements are widely used in industries such as automotive, aerospace, and power generation.
When it comes to high flow filter elements, it is important to consider the specific requirements of your industrial filtration needs. Factors such as flow rate, filtration efficiency, and dirt-holding capacity should be taken into account when selecting the appropriate filter element for your application. Consulting with filtration experts can help you determine the best filter element for your specific needs.
In conclusion, high flow filter elements are the backbone of industrial filtration. They are designed to handle large volumes of fluid while maintaining high levels of filtration performance. Pleated filter cartridges, bag filters, depth filters, and coalescing filter elements are just a few examples of the types of high flow filter elements available for different industrial filtration needs. By selecting the right filter element for your application, you can ensure efficient and effective filtration, leading to improved product quality and process efficiency.
Maintenance and Replacement Tips for High Flow Filter Elements in Industrial Settings
High flow filter elements play a crucial role in industrial filtration systems, ensuring that contaminants are effectively removed from liquids and gases to maintain the quality and efficiency of industrial processes. These filter elements are designed to handle high flow rates, making them ideal for use in industrial settings where large volumes of fluids need to be filtered quickly and efficiently.
One of the key factors to consider when using high flow filter elements in industrial applications is proper maintenance and timely replacement. Regular maintenance of filter elements is essential to ensure optimal performance and prevent system downtime. Over time, filter elements can become clogged with contaminants, reducing their effectiveness and potentially causing damage to the filtration system.
To maintain high flow filter elements in industrial settings, it is important to establish a regular maintenance schedule. This schedule should include routine inspections of the filter elements to check for signs of wear or clogging. In addition, it is important to monitor the pressure drop across the filter elements, as an increase in pressure drop can indicate that the filter elements are becoming clogged and need to be replaced.
When it comes time to replace high flow filter elements in industrial settings, it is important to choose the right replacement filter elements for the specific application. There are a wide variety of high flow filter elements available on the market, each designed to meet the unique filtration needs of different industries. It is important to select filter elements that are compatible with the filtration system and capable of handling the flow rates and contaminants present in the industrial process.
When replacing high flow filter elements, it is important to follow the manufacturer’s recommendations for installation and maintenance. This includes properly installing the filter elements in the filtration system, ensuring that they are securely in place and properly sealed to prevent leaks. It is also important to properly dispose of old filter elements in accordance with local regulations to prevent environmental contamination.
In addition to regular maintenance and timely replacement, there are a few tips that can help extend the life of high flow filter elements in industrial settings. One tip is to use pre-filters or strainers to remove larger particles before they reach the high flow filter elements. This can help reduce the amount of contaminants that the filter elements need to handle, prolonging their lifespan and reducing the frequency of replacement.
Another tip is to monitor the quality of the fluids being filtered and make any necessary adjustments to the filtration system to prevent excessive contamination. By maintaining clean fluids and minimizing the introduction of contaminants into the system, the lifespan of high flow filter elements can be extended, reducing maintenance costs and downtime.
In conclusion, high flow filter elements are the backbone of industrial filtration systems, ensuring that contaminants are effectively removed from liquids and gases to maintain the quality and efficiency of industrial processes. Proper maintenance and timely replacement of filter elements are essential to ensure optimal performance and prevent system downtime. By following the tips outlined in this article, industrial operators can maximize the lifespan of high flow filter elements and keep their filtration systems running smoothly.
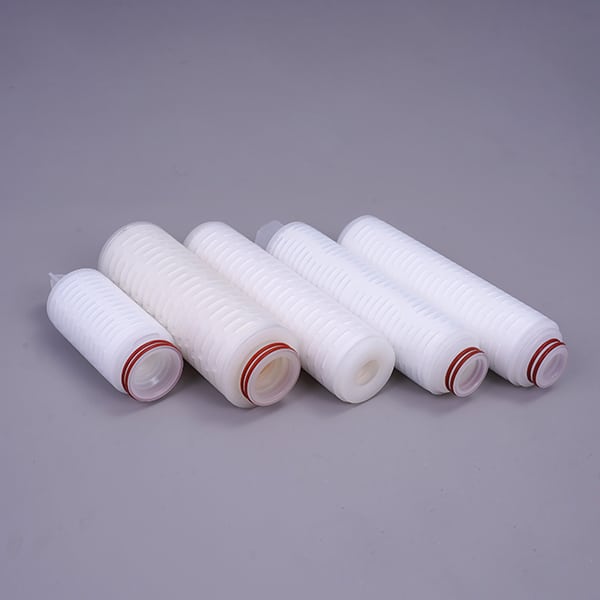