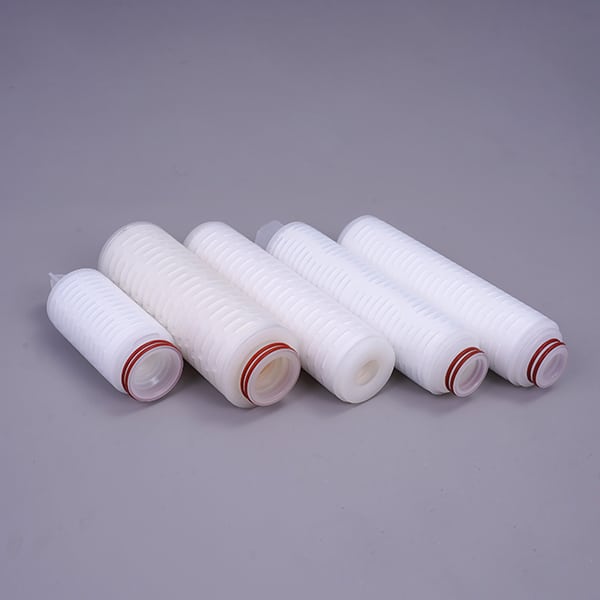
How to Choose the Right Industrial Pleated Filter for Your Factory
Factors to Consider When Selecting an Industrial Pleated Filter
When it comes to maintaining a clean and efficient factory environment, choosing the right industrial pleated filter is crucial. Industrial pleated filters are designed to capture dust, dirt, and other particles from the air, helping to improve air quality and protect equipment from damage. With so many options available on the market, it can be overwhelming to select the best filter for your specific needs. In this article, we will discuss the factors to consider when selecting an industrial pleated filter for your factory.
One of the first factors to consider when choosing an industrial pleated filter is the size of the filter. Industrial pleated filters come in a variety of sizes, so it is important to measure the dimensions of your existing filter or filter housing to ensure a proper fit. A filter that is too small will not effectively capture particles, while a filter that is too large may not fit properly and could lead to air leaks. It is also important to consider the airflow requirements of your equipment when selecting a filter size.
Another important factor to consider is the efficiency rating of the filter. The efficiency rating of a filter indicates how well it can capture particles of a certain size. Filters with higher efficiency ratings are able to capture smaller particles, providing better air quality and equipment protection. It is important to choose a filter with an efficiency rating that meets the needs of your specific application.
In addition to size and efficiency, it is important to consider the material of the filter. Industrial pleated filters are typically made from materials such as polyester, fiberglass, or synthetic fibers. Each material has its own advantages and disadvantages, so it is important to choose a material that is compatible with your specific application. For example, fiberglass filters are durable and resistant to moisture, making them ideal for high-humidity environments.
When selecting an industrial pleated filter, it is also important to consider the operating temperature of your equipment. Some filters are designed to withstand high temperatures, while others may degrade or melt if exposed to extreme heat. It is important to choose a filter that can withstand the temperature conditions of your factory to ensure optimal performance and longevity.
Finally, it is important to consider the cost of the filter. Industrial pleated filters come in a wide range of prices, so it is important to choose a filter that fits within your budget. While it may be tempting to opt for a cheaper filter, it is important to consider the long-term costs of maintenance and replacement. Investing in a high-quality filter may save you money in the long run by reducing equipment downtime and extending the life of your equipment.
In conclusion, choosing the right industrial pleated filter for your factory is essential for maintaining a clean and efficient work environment. By considering factors such as size, efficiency, material, operating temperature, and cost, you can select a filter that meets the needs of your specific application. Taking the time to research and select the best filter for your factory will help to improve air quality, protect equipment, and ensure the smooth operation of your facility.
Comparing Different Types of Industrial Pleated Filters
Industrial pleated filters are an essential component in many factories and industrial settings. They play a crucial role in maintaining air quality, protecting equipment, and ensuring the safety of workers. With so many options available on the market, choosing the right industrial pleated filter for your factory can be a daunting task. In this article, we will discuss the different types of industrial pleated filters available and provide some tips on how to choose the right one for your specific needs.
One of the most common types of industrial pleated filters is the HEPA filter. HEPA filters are highly efficient at capturing small particles, making them ideal for environments where air quality is a top priority. These filters are capable of capturing particles as small as 0.3 microns, making them perfect for removing dust, pollen, and other allergens from the air. HEPA filters are often used in cleanrooms, hospitals, and other sensitive environments where air quality is critical.
Another popular type of industrial pleated filter is the MERV filter. MERV filters are rated on a scale from 1 to 16, with higher ratings indicating better filtration efficiency. These filters are designed to capture a wide range of particles, including dust, pollen, mold spores, and pet dander. MERV filters are commonly used in commercial buildings, schools, and other high-traffic areas where air quality is a concern.
In addition to HEPA and MERV filters, there are also specialty filters available for specific applications. For example, carbon filters are designed to remove odors and gases from the air, making them ideal for environments where chemical fumes or other pollutants are present. Electrostatic filters use an electric charge to attract and capture particles, making them highly efficient at removing dust and other contaminants from the air.
When choosing the right industrial pleated filter for your factory, it is important to consider the specific needs of your environment. If air quality is a top priority, a HEPA filter may be the best option. If you are looking for a more cost-effective solution, a MERV filter may be sufficient for your needs. Specialty filters can be used to address specific concerns, such as odors or chemical pollutants.
It is also important to consider the size and capacity of the filter when making your decision. Industrial pleated filters come in a variety of sizes and configurations, so it is important to choose a filter that is compatible with your existing HVAC system. Additionally, you will need to consider the airflow requirements of your environment to ensure that the filter is able to effectively capture and remove particles from the air.
In conclusion, choosing the right industrial pleated filter for your factory is an important decision that should not be taken lightly. By considering the specific needs of your environment, as well as the size and capacity of the filter, you can ensure that you select a filter that will provide optimal performance and protection for your facility. Whether you choose a HEPA filter, a MERV filter, or a specialty filter, investing in high-quality filtration is essential for maintaining a safe and healthy work environment.
Tips for Maintaining and Replacing Industrial Pleated Filters
Industrial pleated filters play a crucial role in maintaining air quality and ensuring the smooth operation of machinery in factories. These filters are designed to capture dust, dirt, and other particles that can contaminate the air and cause damage to equipment. However, with so many options available on the market, choosing the right industrial pleated filter for your factory can be a daunting task. In this article, we will provide some tips to help you make an informed decision when selecting and replacing industrial pleated filters.
When choosing an industrial pleated filter for your factory, it is important to consider the specific needs of your facility. Different types of filters are designed to capture different sizes of particles, so it is essential to determine the level of filtration required for your application. For example, if your factory produces fine particles that can easily clog filters, you may need a filter with a higher MERV rating to ensure optimal performance.
Another important factor to consider when choosing an industrial pleated filter is the size of the filter. Filters come in a variety of sizes, so it is crucial to measure the dimensions of your existing filter or filter housing to ensure a proper fit. Using a filter that is too small or too large can result in reduced filtration efficiency and increased energy consumption.
In addition to size and filtration efficiency, it is also important to consider the material of the filter. Industrial pleated filters are typically made from materials such as polyester, fiberglass, or synthetic fibers. Each material has its advantages and disadvantages, so it is essential to choose a filter material that is compatible with the specific conditions in your factory.
Once you have selected the right industrial pleated filter for your factory, it is important to establish a regular maintenance schedule to ensure optimal performance. Regular maintenance includes inspecting the filter for damage, cleaning or replacing the filter as needed, and monitoring air quality to ensure that the filter is capturing particles effectively.
When it comes time to replace your industrial pleated filter, it is essential to follow the manufacturer’s recommendations for filter replacement. Most filters have a recommended service life, after which they should be replaced to maintain optimal performance. Ignoring filter replacement can result in reduced filtration efficiency, increased energy consumption, and potential damage to equipment.
In conclusion, choosing the right industrial pleated filter for your factory is essential for maintaining air quality and ensuring the smooth operation of machinery. By considering factors such as filtration efficiency, size, material, and maintenance, you can select a filter that meets the specific needs of your facility. Establishing a regular maintenance schedule and following manufacturer recommendations for filter replacement will help ensure that your industrial pleated filter continues to perform effectively.
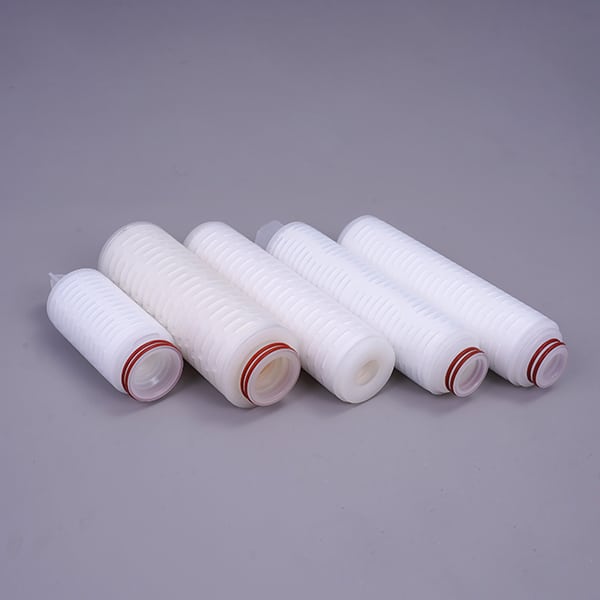