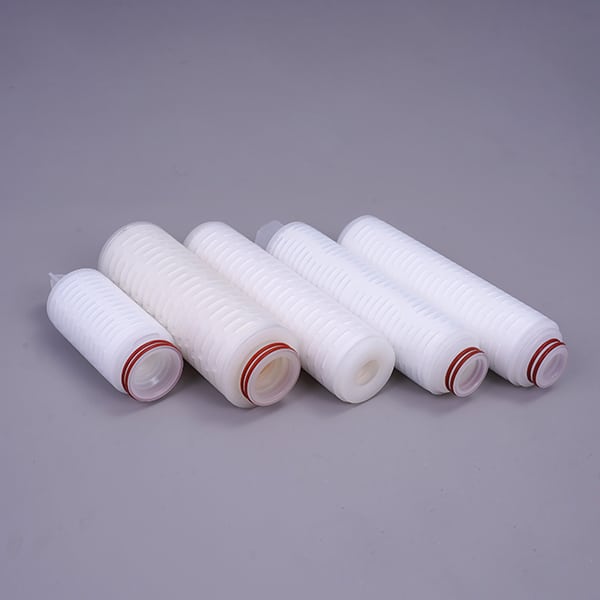
Maximizing Lifespan of High Flow Filter Elements: Tips and Tricks
Benefits of Regular Maintenance for High Flow Filter Elements
High flow filter elements are essential components in many industrial processes, helping to remove contaminants and impurities from liquids and gases. To ensure the optimal performance and longevity of these filter elements, regular maintenance is crucial. By following a few simple tips and tricks, you can maximize the lifespan of your high flow filter elements and keep your equipment running smoothly.
One of the key benefits of regular maintenance for high flow filter elements is the prevention of costly downtime. When filter elements become clogged or damaged, they can impede the flow of liquids or gases through the system, leading to decreased efficiency and potential equipment failure. By regularly inspecting and cleaning your filter elements, you can identify and address any issues before they escalate, minimizing the risk of unexpected breakdowns and production delays.
Another advantage of regular maintenance is the improvement of overall system performance. Clean and properly functioning filter elements allow for optimal flow rates and filtration efficiency, ensuring that your equipment operates at peak performance levels. By maintaining your filter elements on a regular basis, you can maximize the effectiveness of your filtration system and achieve consistent results in your industrial processes.
In addition to preventing downtime and improving performance, regular maintenance can also extend the lifespan of your high flow filter elements. Over time, contaminants and debris can accumulate on the surface of filter elements, reducing their effectiveness and potentially causing damage. By regularly cleaning and replacing filter elements as needed, you can prolong their lifespan and avoid the need for costly replacements.
To maximize the lifespan of your high flow filter elements, it is important to establish a regular maintenance schedule. This schedule should include routine inspections, cleanings, and replacements of filter elements based on manufacturer recommendations and the specific requirements of your equipment. By staying proactive and consistent with your maintenance efforts, you can ensure that your filter elements remain in optimal condition and continue to perform effectively.
When performing maintenance on high flow filter elements, it is important to use the proper tools and techniques to avoid causing damage. Be sure to follow manufacturer guidelines for cleaning and replacing filter elements, and use only recommended cleaning solutions and procedures. Additionally, be mindful of the pressure and flow rates within your system to prevent overloading or damaging the filter elements during maintenance.
In conclusion, regular maintenance is essential for maximizing the lifespan of high flow filter elements and ensuring the continued efficiency and performance of your industrial equipment. By establishing a consistent maintenance schedule, using the proper tools and techniques, and staying proactive in your efforts, you can extend the lifespan of your filter elements and avoid costly downtime and repairs. With proper care and attention, your high flow filter elements can continue to provide reliable filtration and support for your industrial processes for years to come.
Importance of Proper Installation Techniques for High Flow Filter Elements
High flow filter elements are essential components in many industrial processes, helping to remove contaminants and impurities from liquids and gases. To ensure the optimal performance and longevity of these filter elements, proper installation techniques are crucial. In this article, we will discuss the importance of proper installation techniques for high flow filter elements and provide some tips and tricks to help maximize their lifespan.
One of the key factors in ensuring the effectiveness of high flow filter elements is proper installation. Improper installation can lead to leaks, bypass, and reduced filtration efficiency, ultimately shortening the lifespan of the filter element. Therefore, it is essential to follow the manufacturer’s guidelines and recommendations when installing high flow filter elements.
When installing high flow filter elements, it is important to ensure that all connections are tight and secure. Loose connections can lead to leaks, allowing contaminants to bypass the filter element and enter the system. To prevent this, it is recommended to use the appropriate tools and techniques to tighten connections properly.
In addition to ensuring tight connections, it is also important to properly align the filter element within the housing. Misalignment can cause uneven wear and tear on the filter element, reducing its effectiveness and lifespan. To avoid this, carefully follow the manufacturer’s instructions for aligning the filter element within the housing.
Another important aspect of proper installation is ensuring that the filter element is installed in the correct orientation. Installing the filter element upside down or backwards can impede the flow of liquid or gas through the filter, reducing its efficiency. To prevent this, carefully check the orientation of the filter element before installation and make any necessary adjustments.
Properly sealing the filter element within the housing is also crucial for maximizing its lifespan. A secure seal prevents leaks and ensures that all liquid or gas passing through the filter element is properly filtered. To achieve a tight seal, it is recommended to use the appropriate gaskets or O-rings and follow the manufacturer’s guidelines for sealing the filter element within the housing.
In addition to following proper installation techniques, regular maintenance and inspection of high flow filter elements are essential for maximizing their lifespan. Regularly inspecting the filter element for signs of wear or damage, such as tears or holes, can help prevent leaks and ensure optimal filtration performance. Additionally, replacing the filter element at the recommended intervals can help prevent clogging and maintain efficient filtration.
In conclusion, proper installation techniques are essential for maximizing the lifespan of high flow filter elements. By following the manufacturer’s guidelines and recommendations, ensuring tight connections, proper alignment, correct orientation, and secure sealing, you can help prevent leaks, bypass, and reduced filtration efficiency. Additionally, regular maintenance and inspection of the filter element can help identify and address any issues before they escalate. By taking these steps, you can ensure that your high flow filter elements perform optimally and last longer, ultimately saving you time and money in the long run.
How to Choose the Right High Flow Filter Element for Your Application
High flow filter elements are essential components in many industrial applications, helping to remove contaminants and ensure the smooth operation of equipment. To maximize the lifespan of these filter elements, it is crucial to choose the right one for your specific application. In this article, we will discuss some tips and tricks for selecting the best high flow filter element to meet your needs.
When choosing a high flow filter element, the first step is to consider the type of contaminants that need to be removed. Different filter elements are designed to capture specific types of particles, such as dirt, oil, or water. By understanding the nature of the contaminants in your application, you can select a filter element that is most effective at removing them.
Another important factor to consider when choosing a high flow filter element is the flow rate of your system. High flow filter elements are designed to handle a large volume of fluid, so it is essential to select one that can accommodate the flow rate of your equipment. Choosing a filter element that is too small for your system can lead to reduced efficiency and premature clogging, while selecting one that is too large may result in unnecessary pressure drop.
In addition to flow rate, it is also important to consider the pressure rating of the filter element. High flow filter elements are subjected to high pressures in many industrial applications, so it is crucial to choose one that can withstand these conditions. Selecting a filter element with a pressure rating that is too low can lead to leaks and system failures, while choosing one that is too high may result in unnecessary costs.
When selecting a high flow filter element, it is also important to consider the material of construction. Filter elements are available in a variety of materials, including stainless steel, polypropylene, and fiberglass. The material of construction should be selected based on the compatibility with the fluid being filtered and the operating conditions of the system. For example, stainless steel filter elements are ideal for high-temperature applications, while polypropylene filter elements are suitable for filtering corrosive fluids.
In addition to these factors, it is also important to consider the micron rating of the filter element. The micron rating indicates the size of particles that the filter element can capture, with lower micron ratings indicating finer filtration. By selecting a filter element with the appropriate micron rating for your application, you can ensure that it effectively removes contaminants without restricting flow.
In conclusion, choosing the right high flow filter element is essential for maximizing its lifespan and ensuring the efficient operation of your equipment. By considering factors such as the type of contaminants, flow rate, pressure rating, material of construction, and micron rating, you can select a filter element that meets your specific needs. With the right filter element in place, you can improve the performance and longevity of your equipment, ultimately saving time and money in the long run.
Common Mistakes to Avoid When Using High Flow Filter Elements
High flow filter elements are essential components in many industrial processes, helping to remove contaminants and ensure the quality of the final product. However, to maximize the lifespan of these filter elements and maintain their efficiency, it is important to avoid common mistakes that can lead to premature failure.
One common mistake to avoid when using high flow filter elements is failing to properly size the filter for the application. It is important to select a filter element that can handle the flow rate and pressure of the system it is being used in. Using a filter element that is too small for the application can lead to increased pressure drop and reduced efficiency, while using a filter element that is too large can result in bypass and decreased filtration performance.
Another common mistake is failing to properly install the filter element. It is important to follow the manufacturer’s instructions for installation, including ensuring that the filter element is properly seated and sealed in the housing. Improper installation can lead to leaks, bypass, and reduced filtration efficiency.
Failure to properly maintain the filter element is another common mistake that can lead to premature failure. It is important to regularly inspect the filter element for signs of damage or wear, and to replace the element as needed. Additionally, it is important to follow the manufacturer’s recommended maintenance schedule, including cleaning or replacing the filter element at regular intervals.
Using the wrong type of filter element for the application is another common mistake to avoid. There are many different types of filter elements available, each designed for specific applications and contaminants. Using the wrong type of filter element can lead to reduced filtration efficiency and increased maintenance costs.
Failing to monitor the performance of the filter element is another common mistake that can lead to premature failure. It is important to regularly monitor the pressure drop across the filter element, as an increase in pressure drop can indicate that the filter element is becoming clogged and needs to be replaced. Additionally, it is important to monitor the quality of the final product to ensure that the filter element is effectively removing contaminants.
Finally, failing to properly train personnel on the proper use and maintenance of high flow filter elements is another common mistake to avoid. It is important to ensure that all personnel who are responsible for operating and maintaining the filter elements are properly trained on how to do so. This can help to prevent mistakes and ensure that the filter elements are being used and maintained correctly.
In conclusion, maximizing the lifespan of high flow filter elements requires avoiding common mistakes that can lead to premature failure. By properly sizing and installing the filter element, maintaining it regularly, using the correct type of filter element, monitoring its performance, and training personnel on its proper use and maintenance, you can ensure that your filter elements last longer and continue to provide effective filtration.
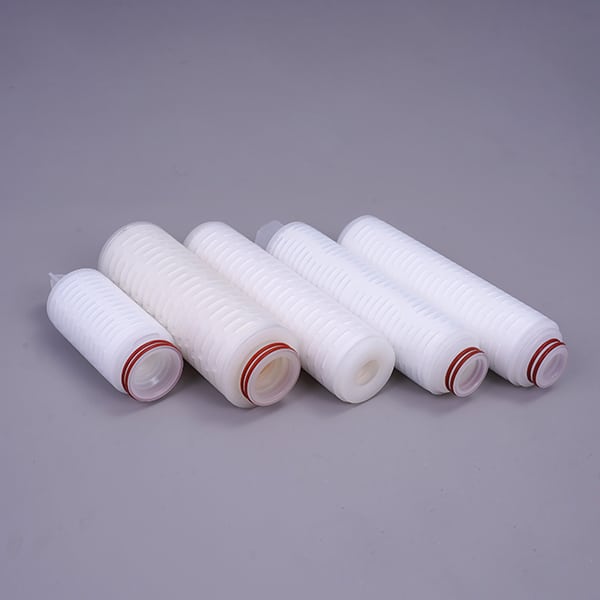