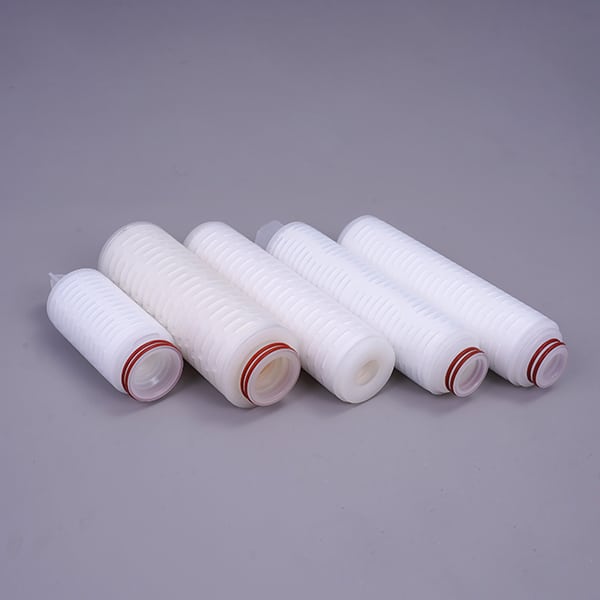
Maximizing System Efficiency with High Flow Pleated Filters for Heavy-Duty Applications
Benefits of Using High Flow Pleated Filters in Heavy-Duty Applications
In heavy-duty applications where efficiency is crucial, the use of high flow pleated filters can make a significant difference in maximizing system performance. These filters are designed to handle high flow rates while maintaining excellent filtration efficiency, making them ideal for demanding industrial environments.
One of the key benefits of using high flow pleated filters is their ability to handle a larger volume of fluid without sacrificing filtration quality. Traditional filters may struggle to keep up with the flow rates required in heavy-duty applications, leading to decreased efficiency and potential system failures. High flow pleated filters, on the other hand, are specifically engineered to handle high flow rates, ensuring that the system operates smoothly and effectively.
Another advantage of high flow pleated filters is their superior filtration efficiency. These filters are designed with a larger surface area and more pleats than traditional filters, allowing them to capture more contaminants and particles from the fluid passing through. This results in cleaner fluid and improved system performance, reducing the risk of equipment damage and downtime.
In addition to their high flow capacity and superior filtration efficiency, high flow pleated filters are also known for their durability and longevity. These filters are constructed from high-quality materials that can withstand the harsh conditions often found in heavy-duty applications. They are designed to resist clogging, tearing, and other forms of damage, ensuring that they can continue to perform effectively over an extended period of time.
Furthermore, high flow pleated filters are easy to install and maintain, making them a convenient choice for busy industrial environments. Their simple design and construction allow for quick and hassle-free installation, while their durable materials and construction reduce the need for frequent replacements or repairs. This not only saves time and money but also ensures that the system remains operational and efficient.
Overall, the benefits of using high flow pleated filters in heavy-duty applications are clear. These filters offer high flow capacity, superior filtration efficiency, durability, and ease of maintenance, making them an excellent choice for maximizing system efficiency in demanding industrial environments. By investing in high flow pleated filters, businesses can ensure that their systems operate at peak performance, reducing the risk of equipment damage, downtime, and costly repairs.
In conclusion, high flow pleated filters are a valuable asset for heavy-duty applications where efficiency is paramount. Their ability to handle high flow rates, provide superior filtration efficiency, and withstand harsh conditions make them an ideal choice for maximizing system performance. By incorporating high flow pleated filters into their systems, businesses can ensure smooth operation, reduced downtime, and improved overall efficiency.
Tips for Selecting the Right High Flow Pleated Filter for Maximum System Efficiency
In heavy-duty industrial applications, maximizing system efficiency is crucial for ensuring optimal performance and reducing downtime. One key component that plays a critical role in system efficiency is the high flow pleated filter. These filters are designed to handle high flow rates while providing excellent filtration efficiency, making them ideal for heavy-duty applications where large volumes of fluid need to be filtered.
When selecting a high flow pleated filter for your system, there are several factors to consider to ensure maximum efficiency. One of the most important factors to consider is the filtration efficiency of the filter. High flow pleated filters are available in various filtration ratings, ranging from coarse to fine, depending on the level of filtration required for your specific application. It is essential to choose a filter with the appropriate filtration rating to effectively remove contaminants and ensure the cleanliness of the fluid being filtered.
Another important factor to consider when selecting a high flow pleated filter is the filter media. The filter media plays a crucial role in determining the filtration efficiency and flow rate of the filter. Different types of filter media, such as cellulose, synthetic, or glass fiber, offer varying levels of filtration efficiency and flow rates. It is essential to choose a filter with the appropriate filter media that can effectively capture contaminants while maintaining a high flow rate to maximize system efficiency.
In addition to filtration efficiency and filter media, the size and design of the high flow pleated filter are also important considerations. The size of the filter should be compatible with the flow rate and pressure requirements of your system to ensure optimal performance. The design of the filter, including the pleat count and spacing, can also impact the filtration efficiency and flow rate of the filter. Choosing a filter with a high pleat count and proper spacing can help maximize filtration efficiency and flow rate, leading to improved system performance.
Furthermore, it is essential to consider the compatibility of the high flow pleated filter with the fluid being filtered. Some fluids may require specialized filter materials or coatings to prevent degradation or contamination. It is crucial to select a filter that is compatible with the specific fluid being filtered to ensure optimal performance and longevity of the filter.
When selecting a high flow pleated filter for heavy-duty applications, it is also important to consider the maintenance requirements of the filter. Regular maintenance, such as filter replacement or cleaning, is essential to ensure the continued efficiency and performance of the filter. Choosing a filter that is easy to maintain and replace can help minimize downtime and reduce maintenance costs in the long run.
In conclusion, selecting the right high flow pleated filter is essential for maximizing system efficiency in heavy-duty applications. By considering factors such as filtration efficiency, filter media, size, design, fluid compatibility, and maintenance requirements, you can choose a filter that will effectively remove contaminants, maintain a high flow rate, and ensure optimal system performance. Investing in a high-quality high flow pleated filter will not only improve system efficiency but also reduce downtime and maintenance costs, ultimately leading to increased productivity and profitability.
Case Studies Demonstrating Improved Performance with High Flow Pleated Filters in Heavy-Duty Applications
In heavy-duty applications where efficiency and performance are crucial, the use of high flow pleated filters has proven to be a game-changer. These filters are designed to handle high flow rates while maintaining excellent filtration efficiency, making them ideal for demanding industrial environments. In this article, we will explore several case studies that demonstrate the significant improvements in system efficiency achieved by using high flow pleated filters.
One such case study involves a manufacturing plant that was experiencing frequent downtime due to clogged filters in their hydraulic systems. The plant decided to switch to high flow pleated filters, which were able to handle the high flow rates of their hydraulic systems while effectively capturing contaminants. As a result, the plant saw a significant reduction in filter changes and downtime, leading to increased productivity and cost savings.
Another case study involves a mining operation that was struggling with high levels of particulate contamination in their lubrication systems. By switching to high flow pleated filters, the mining operation was able to achieve a cleaner lubrication system, resulting in improved equipment performance and reduced maintenance costs. The filters were able to capture even the smallest particles, ensuring that the lubrication systems remained clean and efficient.
In a third case study, a power generation plant was facing challenges with maintaining the cleanliness of their cooling water systems. The plant implemented high flow pleated filters in their cooling water systems, which helped to remove contaminants and improve water quality. This led to improved heat transfer efficiency and reduced corrosion in the plant’s equipment, ultimately extending the lifespan of their cooling systems.
Overall, these case studies highlight the significant impact that high flow pleated filters can have on system efficiency in heavy-duty applications. By choosing the right filter for the job, industrial plants and operations can improve equipment performance, reduce maintenance costs, and increase overall productivity.
In conclusion, high flow pleated filters are a valuable tool for maximizing system efficiency in heavy-duty applications. The case studies discussed in this article demonstrate the tangible benefits of using these filters, from reducing downtime and maintenance costs to improving equipment performance and extending the lifespan of critical systems. By investing in high flow pleated filters, industrial plants and operations can ensure that their systems run smoothly and efficiently, ultimately leading to increased profitability and success.
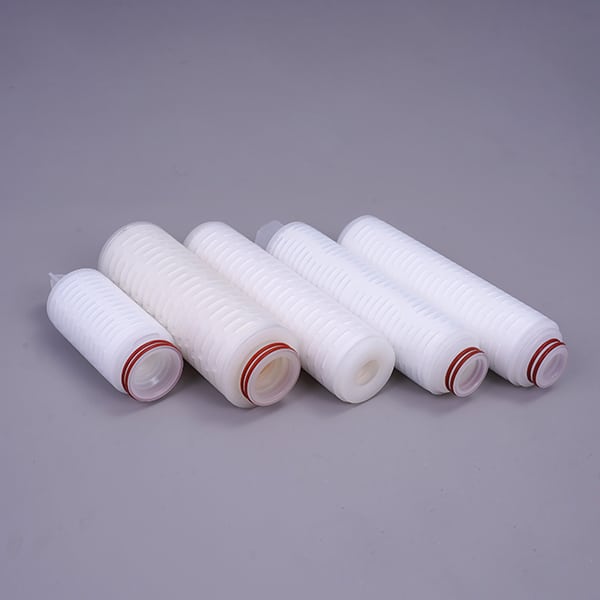