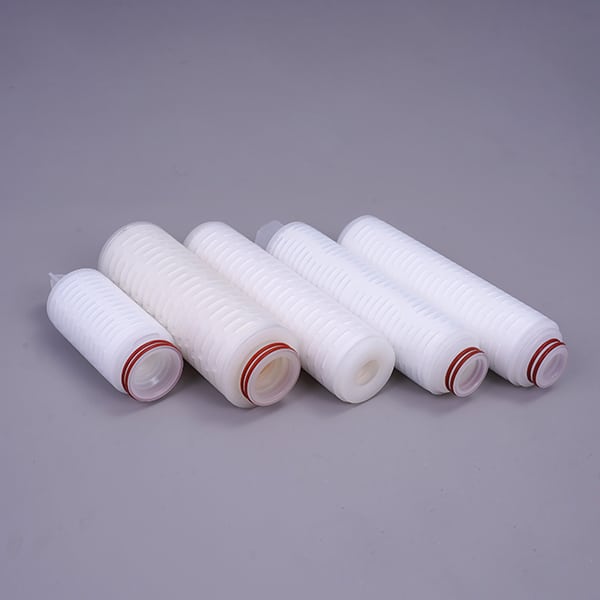
The Role of Industrial Spiral Belts in Modern Manufacturing
Benefits of Using Industrial Spiral Belts in Manufacturing Processes
Industrial spiral belts play a crucial role in modern manufacturing processes, providing a range of benefits that contribute to increased efficiency, productivity, and quality. These specialized belts are designed to handle a variety of materials and products, making them an essential component in industries such as food processing, pharmaceuticals, automotive, and more.
One of the key benefits of using industrial spiral belts is their ability to facilitate the movement of materials through the manufacturing process. These belts are designed to transport products smoothly and efficiently, reducing the risk of damage or contamination. This ensures that products are handled with care and precision, leading to higher quality end products.
In addition to their transport capabilities, industrial spiral belts also play a crucial role in the drying and cooling processes in manufacturing. These belts are often used in ovens and cooling tunnels to facilitate the even distribution of heat or air, ensuring that products are dried or cooled uniformly. This helps to prevent inconsistencies in the final product and ensures that products meet quality standards.
Furthermore, industrial spiral belts are highly durable and resistant to wear and tear, making them a cost-effective solution for manufacturers. These belts are designed to withstand the rigors of industrial use, providing long-lasting performance and reliability. This reduces the need for frequent replacements and maintenance, saving manufacturers time and money in the long run.
Another benefit of using industrial spiral belts is their versatility. These belts can be customized to meet the specific needs of different manufacturing processes, allowing manufacturers to optimize their production lines for maximum efficiency. Whether handling delicate food products or heavy automotive parts, industrial spiral belts can be tailored to ensure smooth and efficient operation.
Moreover, industrial spiral belts are easy to clean and maintain, making them an ideal choice for industries with strict hygiene requirements. These belts are designed to be easily disassembled and cleaned, reducing the risk of contamination and ensuring that products meet regulatory standards. This is particularly important in industries such as food processing and pharmaceuticals, where cleanliness is paramount.
In conclusion, industrial spiral belts play a vital role in modern manufacturing processes, offering a range of benefits that contribute to increased efficiency, productivity, and quality. From facilitating the movement of materials to optimizing drying and cooling processes, these belts are an essential component in a wide range of industries. Their durability, versatility, and ease of maintenance make them a cost-effective solution for manufacturers looking to streamline their production lines and meet the demands of today’s competitive market. By investing in industrial spiral belts, manufacturers can ensure that their operations run smoothly and efficiently, leading to higher quality products and increased customer satisfaction.
How Industrial Spiral Belts Improve Efficiency and Productivity in Modern Manufacturing
Industrial spiral belts play a crucial role in modern manufacturing processes, improving efficiency and productivity in a variety of industries. These belts are commonly used in conveyor systems to transport materials and products through different stages of production. Their unique design allows for smooth and continuous movement, reducing downtime and increasing overall output.
One of the key benefits of industrial spiral belts is their ability to handle a wide range of materials, from small components to large, heavy items. This versatility makes them ideal for use in diverse manufacturing environments, such as food processing plants, automotive factories, and pharmaceutical facilities. By using spiral belts, manufacturers can streamline their operations and ensure a consistent flow of materials throughout the production process.
In addition to their versatility, industrial spiral belts are also known for their durability and longevity. Made from high-quality materials such as stainless steel or plastic, these belts are designed to withstand the rigors of daily use in industrial settings. This durability not only reduces maintenance costs but also minimizes the risk of unexpected breakdowns that can disrupt production schedules.
Furthermore, industrial spiral belts are highly customizable, allowing manufacturers to tailor them to their specific needs and requirements. Whether it’s adjusting the belt width, length, or pitch, these belts can be easily modified to accommodate different types of products and production layouts. This flexibility enables manufacturers to optimize their processes and maximize efficiency in their operations.
Another advantage of industrial spiral belts is their ability to operate at high speeds without compromising accuracy or reliability. This is particularly important in industries where time is of the essence, such as the automotive or electronics sectors. By using spiral belts, manufacturers can increase their throughput and meet tight production deadlines without sacrificing quality.
Moreover, industrial spiral belts are designed to minimize product damage during transportation. Their smooth, continuous surface reduces friction and wear on the materials being conveyed, ensuring that they arrive at their destination in pristine condition. This is especially critical in industries where product quality is paramount, such as the pharmaceutical or aerospace sectors.
In conclusion, industrial spiral belts play a vital role in modern manufacturing by improving efficiency and productivity in a variety of industries. Their versatility, durability, customization options, and high-speed capabilities make them an essential component of conveyor systems used in production facilities worldwide. By investing in industrial spiral belts, manufacturers can streamline their operations, reduce downtime, and increase overall output, ultimately leading to greater profitability and success in today’s competitive marketplace.
The Importance of Choosing the Right Industrial Spiral Belt for Specific Manufacturing Applications
In modern manufacturing, industrial spiral belts play a crucial role in the production process. These belts are used in a variety of industries, including food processing, pharmaceuticals, and automotive manufacturing. They are designed to transport materials through different stages of production, ensuring efficiency and consistency in the manufacturing process.
One of the key factors in ensuring the success of a manufacturing operation is choosing the right industrial spiral belt for specific applications. The type of belt used can have a significant impact on the overall performance of the production line. Factors such as material composition, belt width, and pitch can all affect the efficiency and effectiveness of the belt in a particular application.
When selecting an industrial spiral belt, it is important to consider the specific requirements of the manufacturing process. For example, in food processing, belts must be able to withstand high temperatures and be resistant to oils and greases. In pharmaceutical manufacturing, belts must be able to meet strict hygiene standards and be easy to clean and sanitize. In automotive manufacturing, belts must be able to handle heavy loads and be durable enough to withstand the rigors of the production process.
Another important consideration when choosing an industrial spiral belt is the material composition. Belts can be made from a variety of materials, including stainless steel, carbon steel, and plastic. Each material has its own unique properties that make it suitable for specific applications. For example, stainless steel belts are ideal for applications where hygiene is a priority, while plastic belts are lightweight and flexible, making them suitable for applications where flexibility is important.
The width of the belt is also an important factor to consider when choosing an industrial spiral belt. The width of the belt will determine the amount of material that can be transported at one time. A wider belt will be able to transport larger quantities of material, increasing the efficiency of the production process. However, a wider belt may also require more space and be more expensive to install and maintain.
The pitch of the belt is another important consideration when choosing an industrial spiral belt. The pitch refers to the distance between the individual spirals on the belt. A smaller pitch will result in a tighter mesh, which can be beneficial for applications where small or delicate materials need to be transported. A larger pitch, on the other hand, will result in a looser mesh, which can be beneficial for applications where larger materials need to be transported.
In conclusion, choosing the right industrial spiral belt for specific manufacturing applications is crucial to the success of a production process. Factors such as material composition, belt width, and pitch all play a role in determining the efficiency and effectiveness of the belt in a particular application. By carefully considering these factors and selecting the appropriate belt for the job, manufacturers can ensure that their production processes run smoothly and efficiently.
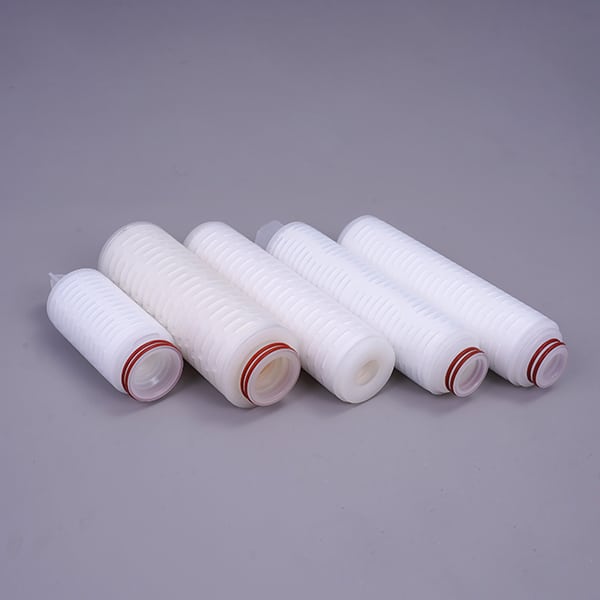