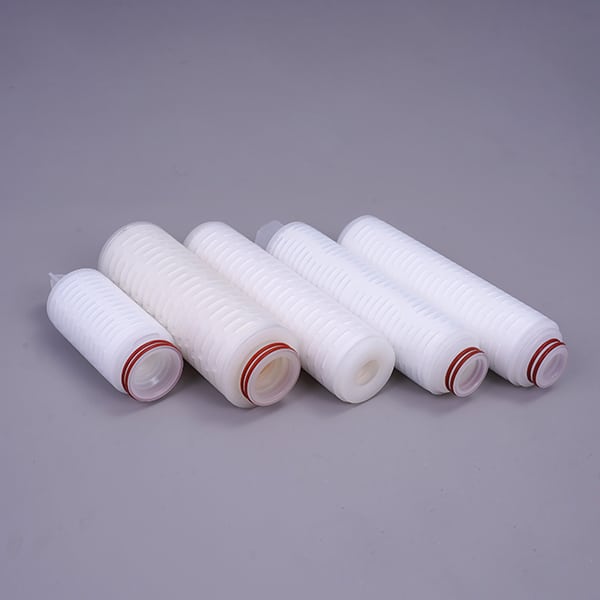
Ultipleat High Flow Filters: Designed for Maximum Efficiency
Advantages of Ultipleat High Flow Filters in Industrial Applications
Ultipleat High Flow Filters have emerged as a pivotal solution in various industrial applications, primarily due to their remarkable efficiency and effectiveness in managing fluid filtration processes. One of the most significant advantages of these filters is their ability to handle high flow rates while maintaining optimal filtration performance. This characteristic is particularly beneficial in industries where large volumes of fluids need to be processed quickly, such as in chemical manufacturing, oil and gas, and water treatment facilities. By accommodating high flow rates, Ultipleat High Flow Filters minimize downtime and enhance productivity, allowing operations to run smoothly and efficiently.
Moreover, the design of Ultipleat High Flow Filters incorporates advanced pleating technology, which maximizes the surface area available for filtration. This increased surface area not only improves the filter’s capacity to capture contaminants but also extends its service life. As a result, industries can experience reduced maintenance costs and less frequent filter replacements, leading to significant savings over time. The longevity of these filters is particularly advantageous in environments where access to filtration systems may be limited or challenging, as it reduces the need for regular interventions.
In addition to their durability, Ultipleat High Flow Filters are engineered to provide superior dirt-holding capacity. This feature is crucial in industrial settings where the presence of particulates can compromise product quality and operational efficiency. By effectively trapping a wide range of contaminants, these filters ensure that the fluids processed remain clean and free from impurities. Consequently, this not only protects downstream equipment from damage but also enhances the overall quality of the end products, thereby meeting stringent industry standards.
Another notable advantage of Ultipleat High Flow Filters is their versatility. They can be utilized in a variety of applications, including but not limited to, hydraulic systems, coolant filtration, and process water treatment. This adaptability makes them an ideal choice for industries that require customized filtration solutions tailored to specific operational needs. Furthermore, the filters are compatible with a range of fluids, including oils, chemicals, and water, which broadens their applicability across different sectors.
The ease of installation and integration of Ultipleat High Flow Filters into existing systems is yet another benefit that cannot be overlooked. Their design allows for straightforward replacement and minimal disruption during installation, which is essential in maintaining continuous operations. This user-friendly aspect is particularly appealing to facilities looking to upgrade their filtration systems without incurring significant downtime or operational delays.
Additionally, Ultipleat High Flow Filters contribute to environmental sustainability efforts within industrial operations. By improving the efficiency of filtration processes, these filters help reduce waste and minimize the environmental impact associated with fluid disposal. The extended service life of the filters also means that fewer materials are consumed over time, aligning with the growing emphasis on sustainable practices in industrial settings.
In conclusion, the advantages of Ultipleat High Flow Filters in industrial applications are manifold. Their ability to handle high flow rates, combined with enhanced dirt-holding capacity and extended service life, positions them as a superior choice for various industries. Furthermore, their versatility, ease of installation, and contribution to sustainability underscore their importance in modern industrial filtration solutions. As industries continue to seek efficient and effective filtration methods, Ultipleat High Flow Filters stand out as a reliable option that meets the demands of today’s fast-paced operational environments.
How Ultipleat High Flow Filters Enhance Process Efficiency
Ultipleat High Flow Filters are engineered to significantly enhance process efficiency across various industrial applications. By utilizing advanced filtration technology, these filters provide a solution that not only meets but often exceeds the stringent demands of modern manufacturing and processing environments. The design of Ultipleat High Flow Filters incorporates a unique pleated structure that maximizes the surface area available for filtration. This increased surface area allows for higher flow rates while maintaining optimal filtration performance, thereby reducing the frequency of filter changes and minimizing downtime.
One of the key advantages of Ultipleat High Flow Filters is their ability to handle large volumes of fluid with minimal pressure drop. This characteristic is particularly beneficial in processes where maintaining consistent flow rates is critical. By ensuring that the fluid can pass through the filter with less resistance, these filters contribute to a more stable and efficient operation. Consequently, industries such as pharmaceuticals, food and beverage, and chemical processing can achieve higher throughput without compromising on the quality of the end product.
Moreover, the materials used in the construction of Ultipleat High Flow Filters are selected for their durability and compatibility with a wide range of fluids. This versatility allows these filters to be employed in various applications, from water treatment to oil and gas processing. The robust design not only enhances the longevity of the filters but also ensures that they can withstand the rigors of demanding environments. As a result, businesses can rely on these filters to provide consistent performance over extended periods, further contributing to overall process efficiency.
In addition to their physical attributes, Ultipleat High Flow Filters are designed with ease of maintenance in mind. The filters can be easily replaced or serviced, which reduces the labor and time associated with maintenance activities. This ease of use is particularly advantageous in facilities where operational efficiency is paramount. By minimizing the time spent on filter maintenance, companies can redirect their resources toward other critical areas of production, thereby enhancing overall productivity.
Furthermore, the filtration efficiency of Ultipleat High Flow Filters plays a crucial role in ensuring product quality. By effectively removing contaminants and particulates from fluids, these filters help maintain the integrity of the final product. This is especially important in industries where even minor impurities can lead to significant quality issues or regulatory non-compliance. By investing in high-quality filtration solutions, companies can safeguard their products and enhance their reputation in the marketplace.
Another noteworthy aspect of Ultipleat High Flow Filters is their contribution to sustainability efforts. By optimizing filtration processes and reducing waste, these filters support environmentally responsible practices. The extended service life of the filters means that fewer replacements are needed, which not only conserves resources but also reduces the environmental impact associated with filter disposal. This alignment with sustainability goals is increasingly important for businesses looking to improve their ecological footprint while maintaining operational efficiency.
In conclusion, Ultipleat High Flow Filters are a vital component in enhancing process efficiency across various industries. Their innovative design, coupled with high filtration performance and ease of maintenance, positions them as a preferred choice for businesses aiming to optimize their operations. By ensuring consistent flow rates, maintaining product quality, and supporting sustainability initiatives, these filters play an essential role in driving efficiency and productivity in today’s competitive landscape. As industries continue to evolve, the importance of reliable and efficient filtration solutions like Ultipleat High Flow Filters will only grow, underscoring their value in modern processing environments.
Maintenance Best Practices for Ultipleat High Flow Filters
Ultipleat High Flow Filters are a critical component in many industrial processes, providing efficient filtration of liquids to ensure the quality and integrity of the final product. These filters are designed to handle high flow rates while maintaining optimal filtration efficiency, making them a popular choice for a wide range of applications.
One of the key features of Ultipleat High Flow Filters is their large surface area, which allows for greater dirt-holding capacity and longer service life. This means less frequent filter changes and reduced downtime, resulting in cost savings for businesses. The design of these filters also ensures uniform flow distribution, preventing channeling and maximizing filtration performance.
In order to maintain the efficiency of Ultipleat High Flow Filters, proper maintenance practices must be followed. Regular inspection of the filters is essential to ensure they are functioning correctly and to identify any potential issues early on. This includes checking for signs of wear or damage, as well as monitoring pressure differentials to determine when a filter change is necessary.
When it comes time to replace a filter, it is important to use genuine Ultipleat High Flow Filter elements to ensure optimal performance. These filters are specifically designed to fit the housing and provide the necessary filtration efficiency, so using non-genuine parts can compromise the integrity of the system. Additionally, following the manufacturer’s recommended change-out intervals is crucial to prevent clogging and maintain consistent filtration performance.
Proper installation of Ultipleat High Flow Filters is also key to their effectiveness. Filters should be installed according to the manufacturer’s instructions, with all connections securely tightened to prevent leaks or bypass. It is important to ensure that the flow direction is correct, as installing the filter backwards can result in poor filtration and reduced efficiency.
Regularly monitoring the performance of Ultipleat High Flow Filters is essential for maintaining optimal filtration efficiency. This includes tracking pressure differentials, flow rates, and overall system performance to identify any potential issues early on. By staying proactive and addressing any issues promptly, businesses can prevent costly downtime and ensure the quality of their final product.
In conclusion, Ultipleat High Flow Filters are designed for maximum efficiency, providing reliable filtration for a wide range of industrial applications. By following proper maintenance practices, businesses can ensure the longevity and effectiveness of these filters, resulting in cost savings and improved product quality. Regular inspection, using genuine parts, proper installation, and monitoring performance are all key components of maintaining Ultipleat High Flow Filters at their peak efficiency. By incorporating these best practices into their maintenance routine, businesses can maximize the performance and lifespan of their filtration systems.
Comparing Ultipleat High Flow Filters to Traditional Filtration Solutions
In the realm of filtration technology, the Ultipleat High Flow Filters stand out as a significant advancement over traditional filtration solutions. These filters are engineered to provide superior performance, particularly in applications requiring high flow rates and efficient contaminant removal. When comparing Ultipleat High Flow Filters to conventional filters, several key differences emerge, highlighting the advantages of this innovative design.
To begin with, the construction of Ultipleat High Flow Filters is fundamentally different from that of traditional filters. While conventional filters often utilize a single-layer media, Ultipleat filters employ a multi-layered pleated design. This pleating increases the surface area available for filtration, allowing for a higher dirt-holding capacity. Consequently, this design not only enhances the filter’s efficiency but also extends its service life, reducing the frequency of replacements and maintenance. In contrast, traditional filters may require more frequent changes, leading to increased operational costs and downtime.
Moreover, the flow dynamics of Ultipleat High Flow Filters contribute significantly to their efficiency. These filters are designed to minimize pressure drop, which is a common issue with traditional filtration systems. A lower pressure drop means that the system can maintain optimal flow rates without requiring additional energy input. This efficiency translates into lower operational costs and a reduced environmental footprint, as less energy is consumed during the filtration process. In comparison, traditional filters often struggle with higher pressure drops, necessitating more powerful pumps and resulting in increased energy consumption.
In addition to their structural advantages, Ultipleat High Flow Filters also excel in their ability to handle a wide range of contaminants. Traditional filters may be limited in their effectiveness against certain types of particles, particularly those that are smaller or more challenging to capture. However, the advanced media used in Ultipleat filters is specifically designed to capture a broader spectrum of contaminants, including fine particulates and microorganisms. This versatility makes them suitable for various applications, from industrial processes to water treatment, where the quality of the output is paramount.
Furthermore, the ease of installation and integration of Ultipleat High Flow Filters into existing systems is another aspect that sets them apart from traditional solutions. Many conventional filters require complex setups and modifications to existing infrastructure, which can lead to increased labor costs and extended downtime during installation. In contrast, Ultipleat filters are designed for straightforward installation, allowing for quick integration into existing systems. This ease of use not only saves time but also minimizes disruption to operations, making them an attractive option for facilities looking to upgrade their filtration systems.
Lastly, the overall cost-effectiveness of Ultipleat High Flow Filters cannot be overlooked. While the initial investment may be higher than that of traditional filters, the long-term savings associated with reduced maintenance, lower energy consumption, and extended service life often outweigh the upfront costs. As industries increasingly prioritize sustainability and efficiency, the Ultipleat High Flow Filters emerge as a forward-thinking solution that aligns with these goals.
In conclusion, when comparing Ultipleat High Flow Filters to traditional filtration solutions, it becomes evident that the former offers numerous advantages in terms of efficiency, versatility, and cost-effectiveness. As industries continue to evolve and demand higher standards of filtration, the Ultipleat High Flow Filters represent a significant step forward in achieving optimal performance and sustainability in filtration technology.
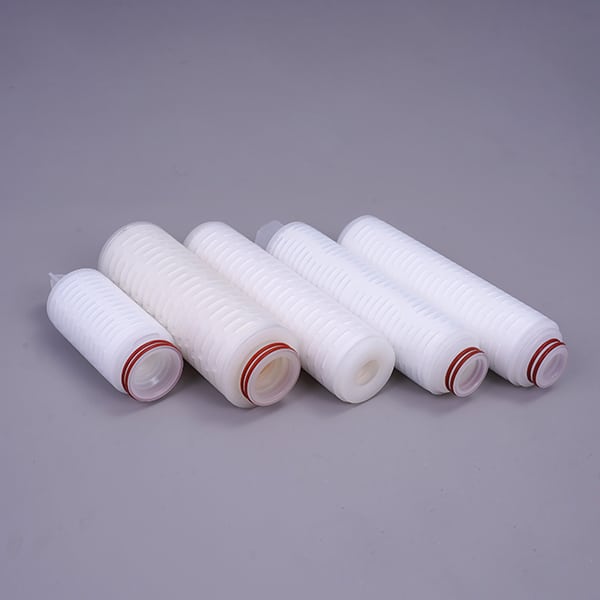