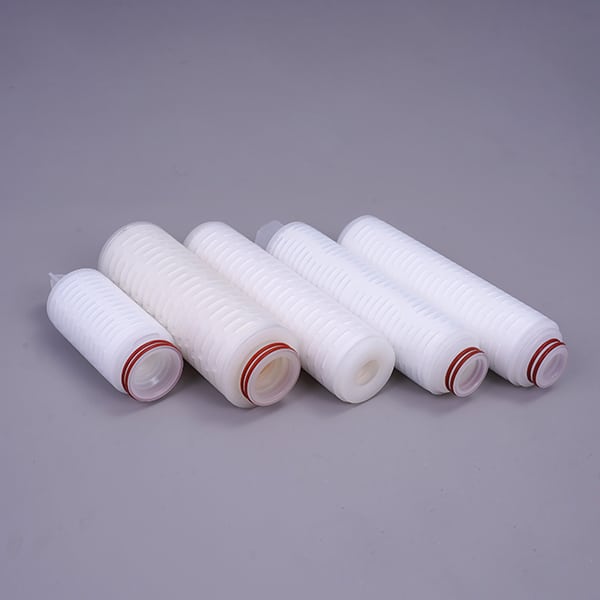
Understanding the Materials Used in High Flow Filter Elements
Types of Materials Used in High Flow Filter Elements
High flow filter elements are essential components in many industrial processes, helping to remove contaminants and impurities from liquids and gases. These filter elements are designed to handle high flow rates while maintaining efficiency and effectiveness. One key factor that determines the performance of high flow filter elements is the materials used in their construction.
There are several types of materials commonly used in high flow filter elements, each with its own unique properties and advantages. Understanding the characteristics of these materials can help users select the right filter element for their specific application.
One of the most common materials used in high flow filter elements is polypropylene. Polypropylene is a thermoplastic polymer that is known for its excellent chemical resistance and thermal stability. It is often used in applications where exposure to harsh chemicals or high temperatures is a concern. Polypropylene filter elements are also lightweight and easy to handle, making them a popular choice for many industrial applications.
Another commonly used material in high flow filter elements is stainless steel. Stainless steel is a durable and corrosion-resistant material that is ideal for applications where cleanliness and hygiene are important. Stainless steel filter elements are often used in food and beverage processing, pharmaceutical manufacturing, and other industries where strict quality control is necessary.
In addition to polypropylene and stainless steel, high flow filter elements can also be made from materials such as polyester, nylon, and ceramic. Each of these materials has its own unique properties that make it suitable for specific applications. For example, polyester filter elements are known for their high dirt-holding capacity and resistance to abrasion, making them a good choice for applications where frequent filter changes are not practical.
Nylon filter elements, on the other hand, are lightweight and have excellent chemical resistance, making them suitable for a wide range of applications. Ceramic filter elements are known for their high temperature resistance and ability to withstand aggressive chemicals, making them ideal for demanding industrial processes.
When selecting a high flow filter element, it is important to consider the specific requirements of the application, as well as the properties of the materials used in the filter element. Factors such as flow rate, pressure drop, temperature, and chemical compatibility should all be taken into account when choosing a filter element.
In conclusion, high flow filter elements play a crucial role in many industrial processes, helping to ensure the quality and purity of liquids and gases. The materials used in these filter elements are key determinants of their performance and effectiveness. By understanding the properties of different materials used in high flow filter elements, users can select the right filter element for their specific application, ensuring optimal performance and efficiency.
Benefits of Using High Quality Materials in Filter Elements
High flow filter elements are essential components in various industries, including water treatment, oil and gas, pharmaceuticals, and food and beverage. These filter elements are designed to remove contaminants and impurities from liquids and gases, ensuring the quality and purity of the final product. One crucial aspect of high flow filter elements is the materials used in their construction. The choice of materials can significantly impact the performance and efficiency of the filter element.
High-quality materials are essential for ensuring the durability and effectiveness of high flow filter elements. The materials used in filter elements must be able to withstand the harsh operating conditions they are subjected to, such as high temperatures, pressure differentials, and corrosive chemicals. Using inferior materials can lead to premature failure of the filter element, resulting in increased maintenance costs and downtime.
One of the most common materials used in high flow filter elements is stainless steel. Stainless steel is known for its excellent corrosion resistance, strength, and durability, making it an ideal choice for filter elements that are exposed to harsh environments. Stainless steel filter elements can withstand high temperatures and pressure differentials without deforming or breaking, ensuring long-term reliability and performance.
Another important material used in high flow filter elements is polypropylene. Polypropylene is a thermoplastic polymer that is lightweight, chemically resistant, and cost-effective. Polypropylene filter elements are commonly used in applications where corrosion resistance and chemical compatibility are essential. These filter elements are suitable for filtering a wide range of liquids and gases, making them versatile and practical for various industries.
In addition to stainless steel and polypropylene, high flow filter elements can also be constructed using other materials such as ceramic, fiberglass, and polyester. Each material has its unique properties and advantages, depending on the specific requirements of the application. For example, ceramic filter elements are known for their high temperature resistance and excellent chemical compatibility, making them suitable for demanding industrial processes.
Using high-quality materials in filter elements offers several benefits. Firstly, high-quality materials ensure the longevity and reliability of the filter element, reducing the need for frequent replacements and maintenance. This can result in cost savings for the end user and improved operational efficiency.
Furthermore, high-quality materials can enhance the filtration performance of the filter element. Materials with high porosity and permeability can effectively capture and retain contaminants, ensuring the purity and quality of the filtered product. This is particularly important in industries such as pharmaceuticals and food and beverage, where product quality and safety are paramount.
In conclusion, understanding the materials used in high flow filter elements is crucial for ensuring their performance and efficiency. High-quality materials such as stainless steel, polypropylene, ceramic, and fiberglass offer durability, reliability, and enhanced filtration performance. By choosing filter elements constructed with high-quality materials, industries can achieve optimal filtration results, reduce maintenance costs, and improve overall operational efficiency.
Factors to Consider When Selecting Materials for High Flow Filter Elements
High flow filter elements are essential components in many industrial processes, helping to remove contaminants and impurities from liquids and gases. When selecting materials for high flow filter elements, there are several factors to consider to ensure optimal performance and longevity.
One of the most important factors to consider when choosing materials for high flow filter elements is the compatibility with the fluid or gas being filtered. Different materials have varying levels of resistance to different chemicals and temperatures, so it is crucial to select materials that will not degrade or react with the fluid or gas being filtered. For example, if the filter element will be used to filter corrosive chemicals, it is important to choose materials that are resistant to corrosion, such as stainless steel or polypropylene.
Another important factor to consider when selecting materials for high flow filter elements is the filtration efficiency. The material used in the filter element should be able to effectively capture and retain contaminants of the desired size. Materials with smaller pore sizes are typically more effective at capturing smaller particles, while materials with larger pore sizes are better suited for capturing larger particles. It is important to consider the size and type of contaminants that need to be removed when selecting materials for high flow filter elements.
In addition to compatibility and filtration efficiency, durability is also an important factor to consider when selecting materials for high flow filter elements. The material used in the filter element should be able to withstand the operating conditions and pressures of the system without degrading or failing. Materials that are resistant to abrasion, corrosion, and high temperatures are typically more durable and long-lasting. It is important to choose materials that will provide reliable performance over an extended period of time.
Cost is another factor to consider when selecting materials for high flow filter elements. Different materials have varying costs, so it is important to balance performance and durability with budget constraints. While high-quality materials may be more expensive upfront, they can provide cost savings in the long run by reducing maintenance and replacement costs. It is important to consider the total cost of ownership when selecting materials for high flow filter elements.
Overall, selecting the right materials for high flow filter elements is crucial to ensuring optimal performance and longevity. By considering factors such as compatibility, filtration efficiency, durability, and cost, you can choose materials that will meet the specific requirements of your application. It is important to work with a trusted supplier or manufacturer to ensure that the materials used in the filter elements are of high quality and meet your specific needs. With the right materials, high flow filter elements can effectively remove contaminants and impurities, helping to improve the efficiency and reliability of industrial processes.
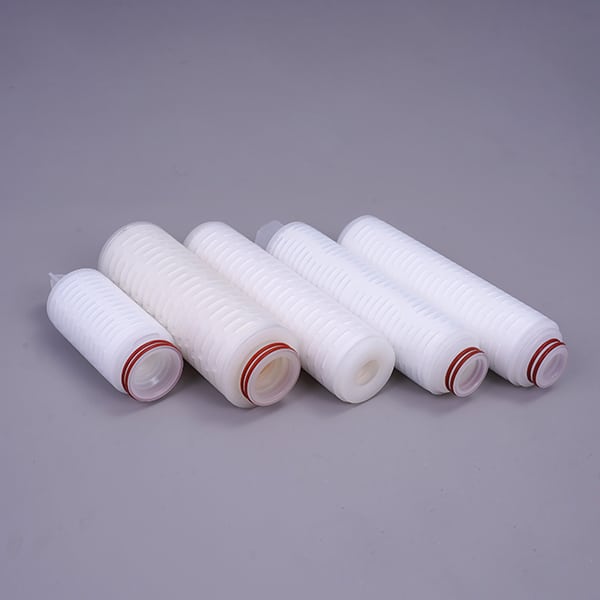